基于UG的變速齒輪箱體數(shù)控加工生產線的設計畢業(yè)設計說明書
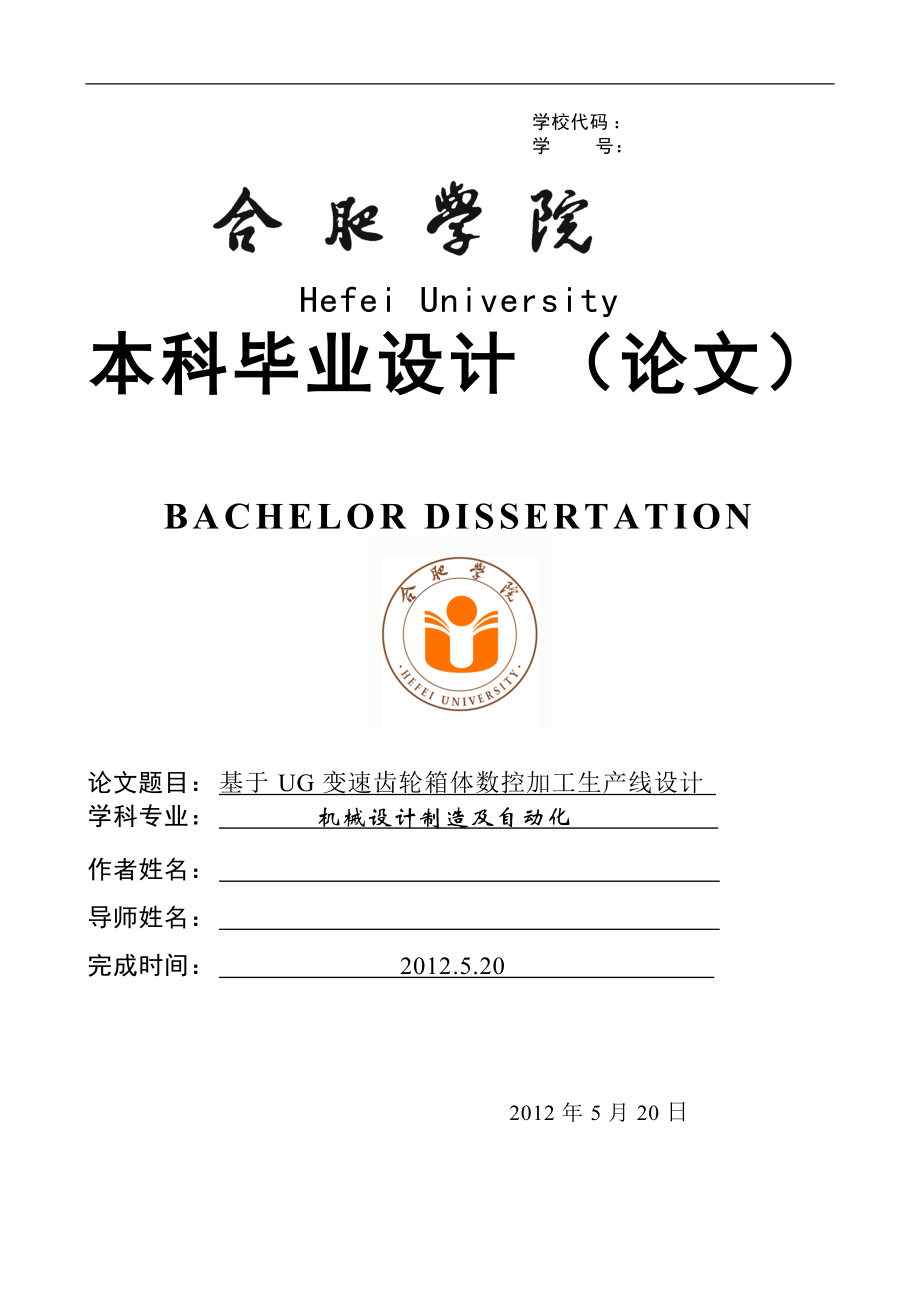


《基于UG的變速齒輪箱體數(shù)控加工生產線的設計畢業(yè)設計說明書》由會員分享,可在線閱讀,更多相關《基于UG的變速齒輪箱體數(shù)控加工生產線的設計畢業(yè)設計說明書(53頁珍藏版)》請在裝配圖網(wǎng)上搜索。
1、 學校代碼 : 學 號:Hefei University本本科科畢畢業(yè)業(yè)設設計計 (論論文文)BACHELOR DISSERTATION論文題目:基于 UG 變速齒輪箱體數(shù)控加工生產線設計學科專業(yè): 機械設計制造及自動化 作者姓名: 導師姓名: 完成時間: 2012.5.20 2012 年 5 月 20日基基于于 U UG G 變變速速齒齒輪輪箱箱體體數(shù)數(shù)控控加加工工生生產產線線設設計計摘摘 要要 加工中心簡稱 CNC。是一種 由機械設備與數(shù)控系統(tǒng)組成的使用于加工復雜形狀工件的高效率自動化機床。 加工中心的突出特點為加工工序集中和能夠實現(xiàn)自動換刀,對于形狀復雜、精度要求較高和要求換刀頻繁的零件
2、的加工能夠提高生產效率、縮短生產周期以獲得較好的經濟效果。本次設計 針對的零件為三星齒輪箱體,形狀復雜、有一定的精度要求并且加工工序較多,因而選擇在加工中心上加工很合適。設計首先用 UG 軟件繪制零件圖、毛坯圖,然后 對零件進行分析 ,確定合適的加工工序,根據(jù)工序選擇相應的定位基準,制定加工工藝,選擇切削用量并計算基本工時,用AutoCAD 繪制加工工藝綜合卡,用 UG 導出其中一道工序的數(shù)控加工 G 代碼,選擇兩道加工工序設計夾具并用CAD 繪制夾具裝配圖 。 關關鍵鍵詞詞:三三星星齒齒輪輪箱箱體體;工工藝藝;工工序序;加加工工中中心心;夾夾具具UG-based Design of CNC
3、Machining Production Line of the Gear Box ABSTRACT Processing center referred to as CNC. Composed by mechanical equipment and numerical control systems used for processing complex shape of workpiece, CNC is a kind of high efficiency automation machine tools. Processing operations focused and able to
4、 achieve automatic tool change is a prominent characteristic of the machining center. When used to process workpieces which are of complex shape, of high accuracy and require for frequent tool change, it can improve production efficiency, shorten the production cycle in order to obtain better econom
5、ic effects.This design is for partNorton gear box who have complex shape, certain degree of accuracy and more processing process.So it is relatively appropriate to process in the processing center.The first step of this design is to use UG to draw the part drawing, blank drawing and process work pre
6、face diagram. Then analysing the part so as to determine appropriate manufacturing procedure, using the UG software export procedure of NC machining process, selecting the appropriate location basis to develop a process route, choosing processing equipment and tools, fixtures, measuring, and calcula
7、ting each procedure of the basic working hours, drawing processing process card. Finalize the fixture design of two process and complete the fixture drawings with CAD. KEY WORD: Norton gear box;technology;process;processing center; fixture ii目目錄錄前前 言言.IV第第 1 1 章章 零零件件分分析析 .11.1. 零件作用分析 .11.2. 零件工藝分析
8、 .2第第 2 2 章章 確確定定毛毛坯坯尺尺寸寸 .32.1. 確定毛坯尺寸 .3第第 3 章章 工工藝藝過過程程設設計計 .43.1. 定位基準的選擇 .43.2. 制定工藝路線 .43.3. 選擇加工設備及刀具 .63.4. 加工工序設計 .12第第 4 4 章章 三三星星齒齒輪輪箱箱體體夾夾具具設設計計 .304.1. 夾具設計的相關要求 .304.2. 定位夾緊方案的確定 .304.3. 切削力及夾緊力的分析 .324.4. 定位誤差分析 .37第第 5 5 章章 銑銑削削下下底底面面 G G 代代碼碼 .39第第 6 6 章章 結結 論論 .45參參考考文文獻獻 .46致致 謝謝
9、.47前前 言言本次設計是在我們學完了大學的全部基礎課,技術基礎課以及專業(yè)課之后而進行。此次的設計是對大學期間所學各課程及相關的應用繪圖軟件的一次深入的綜合性的總復習,也是一次理論聯(lián)系實際的訓練。其目的在于:1鞏固我們在大學里所學的知識,也是對以前所學知識的綜合性的檢驗;2加強我們查閱資料的能力,熟悉有關資料;3樹立正確的設計思想,掌握設計方法,培養(yǎng)我們的實際工作能力;4.能根據(jù)被加工零件的技術要求,運用夾具設計的基本原理和方法,學會擬定夾具設計方案,完成夾具結構設計,初步具備設計出高效,省力,經濟合理并能保證加工質量的專用夾具的能力。5通過零件圖,裝配圖繪制,使我們對于UG 和 AutoCA
10、D 等繪圖軟件的使用能得到進一步的提高。本次設計的主要內容為:首先運用UG 軟件繪制 三星齒輪箱體的三維零件圖立體模型 ,然后根據(jù)圖紙的技術要求等確定生產類型,經分析本次設計的零件年產量為 6000 件,屬大批量生產。其次進行工藝分析,確定零件的數(shù)控加工工藝路線,完成機械加工工序設計 以及數(shù)控加工中心對零件的機加工編程 。最后,對某 兩道加工工序進行夾具裝配圖的設計。機械畢業(yè)設計0第第 1 1 章章 零零件件分分析析1 1. .1 1. . 零零件件作作用用分分析析箱體零件是機器或部件的基礎零件 ,它把有關零件聯(lián)結成一個整體 ,使這些零件保持正確的相對位置 ,彼此能協(xié)調地工作 .因此,箱體零件
11、的制造精度將直接影響機器或部件的裝配質量 ,進而影響機器的使用性能和壽命 .因而箱體一般具有較高的技術要求 。由于機器的結構特點和箱體在機器中的不同功用,箱體零件具有多種不同的結構型式,其共同特點是 :結構形狀復雜 ,箱壁薄而不均勻 ,內部呈腔型 ;有若干精度要求較高的平面和孔系 ,還有較多的緊固螺紋孔等 。毛坯的鑄造方法 ,取決于生產類型和毛坯尺寸 ,在單件小批生產中 ,多采用木模手工造型 ;在大批量生產中廣泛采用金屬模機器造型 ,毛坯的精度較高 ,箱體上大于3050mm 的孔,一般都鑄造出頂孔 ,以減少加工余量 。此畢業(yè)設計零件為三星齒輪箱體,材料為合金鑄鋁,其零件圖如下 . 圖 1.1
12、三星齒輪箱體機械畢業(yè)設計11 1. .2 2. .零零件件工工藝藝分分析析零件三星齒輪箱體的材料 為合金鑄鋁 。該零件上主要加工面為 箱體下底面,50.4mm和86.8mm所在環(huán)形凸臺在箱體外部的 上端面,56mm與65.8mm所成的臺階面,65.8mm內圓表面,56mm與128.8mm在箱體上表面所成的環(huán)形凸臺面 ,77mm與126mm在箱體外側所成的環(huán)狀凸臺 ,2- 12mm孔和7mm孔所在的箱體內部三個凸耳下表面,420mm所在凸臺上表面,77mm孔,56mm孔,50.4mm孔,4個加強肋終端的48M螺紋孔,外部環(huán)形凸臺與內部四耳花型凸臺相連的48M螺紋孔,側面環(huán)狀凸臺上的410M螺紋孔
13、,與下底面凸緣相連的78M螺紋孔、12M螺紋孔,箱體內側三個凸耳上的212M和8M螺紋孔,7mm工藝孔,12 10mm矩形孔,0.10163.6內圓表面與其端面的垂直度為0.05,孔0.03077與孔0.080.02372.8的軸心線不相交度為 0.03,孔0.080.02372.8與內表面0.10163.6的同心度為 0.02。機械畢業(yè)設計2第第 2 2 章章 確確定定毛毛坯坯尺尺寸寸2 2. .1 1. .確確定定毛毛坯坯尺尺寸寸 零件材料 為合金鑄鋁 ,已知零件的生產綱領為 6000 件/年,其生產類型為大批 量生產,毛坯的鑄造方法選用砂型機器造型 及殼型。此外,為消除殘余應力,鑄造后安
14、排人工時效處理。 由機械制造工藝設計簡明手冊 第 38 頁表 2.2-3 可查得尺寸公差等級 CT79 級,選擇 8 級,由機械制造工藝設計簡明手冊 第 41 頁表 2.2-5 可查得加工余量等級 MA 為 G,第 74 頁加工余量表 2.321 可得86.8mm所在環(huán)形凸臺加工余量數(shù)值 2.5mm,下底面加工余量 5.0mm,128.8mm在箱體上表面所成的環(huán)形凸臺面余量為 3.0mm,56mm與65.8mm所成的臺階面余量為 2.5mm,65.8mm內圓表面單邊余量為 2mm,126mm在箱體側面所成的環(huán)狀凸臺余量為3.0mm,420mm所在凸臺表面余量為 2.5mm,2- 12mm孔和7
15、mm孔所在的箱體內部三個凸耳表面余量為2.5mm,77mm孔單邊余量為 2mm,56mm孔單邊余量為 2mm,50.4mm孔單邊余量為 2mm,72.8mm內圓柱面單邊余量為 2mm。圖 2.1 三星齒輪箱體毛坯圖 3第第 3 3 章章 工工藝藝過過程程設設計計3 3. .1 1. .定定位位基基準準的的選選擇擇精基準的選擇: 三星齒輪箱體 的下端面既是裝配基準又是設計基準,用它作為精基準,能使加工遵循 “基準重合 ”的原則,避免產生基準不重合誤差 。50.4mm孔、上表面各凸臺 、4 個加強肋終端的48M螺紋孔,外部環(huán)形凸臺與內部四耳花型凸臺相連的48M螺紋孔,側面環(huán)狀凸臺上的410M螺紋孔
16、及77mm與126mm在箱體外側所成的環(huán)狀凸臺 的加工都采用下底面和底面兩孔 作為基準,這使得工藝路線又遵循 “基準統(tǒng)一”的原則, 避免了產生基準轉換誤差,下底面覆蓋 面積較大,定位比較穩(wěn)定,夾緊方案也比較簡單,可靠,操作方便。粗基準的選擇 :在保證各加工面均有加工余量的前提下,使重要孔或面的加工余量盡量均勻,此外,還要保證定位夾緊的可靠性,裝夾的方便性,減少輔助時間,因而粗基準選為173.6mm箱體外圓弧 面部分和50.4mm和86.8mm所在環(huán)形凸臺的 上表面,采用 V 形塊和圓頭支撐釘 夾持定位。3 3. .2 2. .制制定定工工藝藝路路線線根據(jù)各表面 、孔的加工要求,和各種加工方法能
17、達到的經濟精度,可確定各表面及孔的加工方法如下 .表 3.1 零件加工方案表待 加 工 部 分加 工 方 案下底面粗銑、半精銑、精銑作為精基準的 2-M8 螺紋孔鉆孔、鉸孔、攻絲不作為精基準 6-M8 螺紋孔鉆孔、攻絲7mm孔、3-M12 螺紋孔鉆孔、攻絲86.8mm凸臺表面粗銑、半精銑、精銑420mm所在凸臺表面粗銑420mm凸臺上的48M螺紋孔鉆孔、攻絲128.8mm凸臺表面粗銑、精銑機械畢業(yè)設計450.4mm孔粗鏜56mm孔粗鏜65.8mm內圓表面粗鏜、半精鏜128.8mm凸臺上410M螺紋孔鉆孔、攻絲箱體內部三個凸耳表面粗銑、精銑72.8mm內圓面粗鏜、半精鏜50.4mm與72.8mm
18、所成的臺階面粗鏜、半精鏜 12 10mm矩形槽粗銑126mm凸臺表面粗銑、精銑77mm孔粗鏜126mm凸臺上410M螺紋孔鉆孔、攻絲表 3.2 加工工序工序表工 序 號工 序 內 容定 位 基 準01鑄造02時效粗銑、半精銑、精銑下 底面86.8mm凸臺表面03鉆6-M8孔、7mm孔、鉆鉸作為精基準的2-M8孔、鉆并攻絲3-M12孔86.8mm凸臺表面粗銑、半精銑、精銑86.8mm凸臺表面下底面和2-M8孔420mm所在凸臺表面下底面和2-M8孔鉆攻絲420mm凸臺上的48M螺紋孔下底面和2-M8孔粗銑、精銑128.8mm凸臺表面下底面和2-M8孔鏜50.4mm內圓面下底面和2-M8孔鏜56m
19、m孔下底面和 2-M8 孔鏜65.8mm內圓表面下底面和 2-M8 孔04鉆并攻絲410M螺紋孔下底面和 2-M8 孔 5粗銑、精銑 內部三個凸耳表面86.8mm凸臺表面鏜72.8mm內圓面及50.4mm與72.8mm所成的臺階面86.8mm凸臺表面05 12 10mm矩形槽86.8mm凸臺表面粗銑、精銑126mm凸臺表面下底面和2-M8孔鏜77mm孔下底面和2-M8孔06鉆、攻絲126mm凸臺上410M螺紋孔下底面和2-M8孔07攻絲8-M8螺紋孔86.8mm凸臺表面及50.4mm孔08入庫3 3. .3 3. .選選擇擇加加工工設設備備及及刀刀具具根據(jù)零件加工要求 ,加工設備 選擇數(shù)控加工
20、中心 ,工件在 加工中心 上的裝卸由人工完成。銑銑下下底底面面:根據(jù)加工工序選擇功率為 15KW 的加工中心。由于銑削下底面的夾具夾持不便于采用大直徑的盤銑刀一次橫向一次銑削,故采用小直徑的端銑刀沿著箱體下底面邊緣軌跡銑削,下底面邊緣最寬處寬度約為30mm,則銑削寬度=30mm60mm,由切削用量簡明手冊 第 84 頁表 3.1 和機械制造工ae藝設計簡明手冊 第 100 頁表 3.1-28 知應選用直徑 d=5080mm 的硬質合金鑲齒套式面銑刀。 雖然下底面表面粗糙度要求僅12.5,但要作為精基準,故表面粗糙度至少需要達到 3.2,銑削深度8mm,銑削寬度=30mm60mm,查切削用量簡明
21、手冊 第 84 頁ae表 3.1 和切削用量簡明手冊 第 96 頁表 3.16 知選用=80mm 的硬質合金端銑刀。0d由于合金鑄鋁硬度 40110HBS,小于 220HBS,因而由 切削用量簡明手冊 第 6 頁表 1.2 選擇硬質合金牌號為 YG6 的硬質合金刀片,由 切削用量簡明手冊 第 96 頁表 3.16 知齒數(shù)為 10;查切削用量簡明手冊 第 84 頁表 3.2,由于合金鑄鋁硬度 110HBS150HBS,而銑削余量較小,則銑刀主偏角,過渡刃偏角,副偏角,45kr30kr5kr機械畢業(yè)設計6,0801020s 015鉆鉆 6 6- -M M8 8 孔孔、7mm孔孔、鉆鉆鉸鉸 2 2-
22、 -M M8 8 孔孔、鉆鉆攻攻絲絲 3 3- -M M1 12 2 孔孔: 作為精基準兩孔表面粗糙度至少需要達到3.2 m,但由于各孔徑均小于1520mm,故查機械制造工藝設計簡明手冊 第 20 頁表 1.4-7 知對于作為精基準的兩孔只需要經過鉆孔、鉸孔、攻絲三次加工,經濟精度為IT810 級。而其余諸孔只需要經過鉆孔、攻絲即可。由于作為精基準的兩孔不便于在此道工序就進行攻絲,故此道工序對于 8-M8 螺紋孔只進行其中 6-M8 螺紋孔的鉆孔和作為精基準的2-M8 螺紋孔的鉆孔、鉸孔,對于 3-M12 螺紋孔在此道工序即進行鉆孔和攻絲加工。鉆孔:由 機械制造工藝設計簡明手冊 第 70 頁表
23、 2.3-20 知 M8 螺紋孔攻絲前鉆孔用麻花鉆鉆頭直徑有 為 6.8mm,M12 螺紋孔攻絲前 鉆孔用麻花鉆鉆頭直徑有 為10.2mm,由機械制造工藝設計簡明手冊 第 84 頁表 3.1-6 知硬質合金錐柄麻花鉆直徑系列有 d=6.5mm、6.8mm、10.2mm,因而對于不作為精基準的6-M8 螺紋孔鉆孔時選擇直徑 d=6.8mm 硬質合金錐柄麻花鉆,而7mm孔無需攻絲,且只需要粗加工即可,故對于7mm孔鉆孔時選擇直徑為 d=7mm 硬質合金錐柄麻花鉆,對于需要作為精基準的2-M8 螺紋孔鉆孔時選擇直徑為 d=6.5mm 的硬質合金 錐柄麻花鉆,為鉸孔留下余量,而對于 3-M12 螺紋孔
24、鉆孔時選擇直徑為 d=10.2mm 硬質合金錐柄麻花鉆。由于被加工材料為合金鑄鋁,由 切削用量簡明手冊 第 46 頁表 2.2 知鉆頭幾何參數(shù)分別為,取為;290 140118鉸孔:由于被加工材料為合金鑄鋁,硬度較小,故可選擇高速鋼鉸刀,需要做鉸孔處理的為 2-M8 孔,鉸刀 直徑為 d=6.8mm,由切削用量簡明手冊 第 49 頁表 2.6 選擇的鉸刀幾何參數(shù)后角為010 12,齒背傾斜角為115 20,由于在加工中心上加工,則機用鉸刀主偏角;60kr攻絲: 對于 3-M12 螺紋孔在此道工序即進行攻絲加工, 由于在之前已經將待加工3-M12 螺紋孔孔徑鉆至 10.2mm,則可根據(jù)相應的直徑
25、參數(shù)選擇對應的絲錐進行攻絲加工。銑銑削削86.8mm凸凸臺臺表表面面:機床仍然為上述相同的加工中心 。因銑削寬度=86.8mm120mm,由切削用量ae簡明手冊 第 84 頁表 3.1 和機械制造工藝設計簡明手冊 第 100 頁表 3.1-28 知應選用直徑 d=100200mm 的硬質合金鑲齒套式面銑刀。 已知總余量為 2.5mm,則銑削深度6mm,銑削寬度=86.8mm120mm,查切削ae用量簡明手冊 第 84 頁表 3.1 和切削用量簡明手冊 第 96 頁表 3.16 知選用=125mm 的硬質合金端銑刀。由于 合金鑄鋁 硬度 40110HBS,小于 220HBS,因而由0d切削用量簡
26、明手冊 第 6 頁表 1.2 選擇硬質合金牌號為 YG6 的硬質合金刀片,由切削用量簡明手冊 第 96 頁表 3.16 知齒數(shù)為 12; 7查切削用量簡明手冊 第 84 頁表 3.2,由于合金鑄鋁 硬度 110HBS150HBS,而銑削余量較小,則銑刀主偏角,過渡刃偏角,副偏角,45kr30kr5kr,0801020s 015粗粗銑銑420mm所所在在凸凸臺臺表表面面:機床仍然為上述相同的加工中心 。因銑削寬度=20mm60mm,由切削用量簡ae明手冊第 84 頁表 3.1 和機械制造工藝設計簡明手冊 第 101 頁表 3.1-28 知應選用直徑 d=5080mm 的硬質合金鑲齒套式面銑刀。
27、已知總余量為 2.5mm,則銑削深度6mm,銑削寬度=20mm60mm,查切削用ae量簡明手冊 第 84 頁表 3.1 和切削用量簡明手冊 第 96 頁表 3.16 知選用=80mm 的硬質合金端銑刀。由于 合金鑄鋁 硬度 40110HBS,小于 220HBS,因而由0d切削用量簡明手冊 第 6 頁表 1.2 選擇硬質合金牌號為 YG6 的硬質合金刀片,由切削用量簡明手冊 第 96 頁表 3.16 知齒數(shù)為 10; 查切削用量簡明手冊 第 84 頁表 3.2,由于合金鑄鋁 硬度 110HBS150HBS,而銑削余量較小,則銑刀主偏角,過渡刃偏角,副偏角,45kr30kr5kr,0801020s
28、 015鉆鉆并并攻攻絲絲420mm凸凸臺臺上上的的48M螺螺紋紋孔孔: 由于各孔徑均小于 1520mm,故查機械制造工藝設計簡明手冊 第 20 頁表1.4-7 知對于各孔只需要經過鉆孔后即可攻絲,經濟精度為IT810 級。鉆孔:由 機械制造工藝設計簡明手冊 第 70 頁表 2.3-20 知 M8 螺紋孔攻絲前鉆孔用麻花鉆鉆頭 直徑有為 6.8mm,由機械制造工藝設計簡明手冊 第 84 頁表3.1-6 知硬質合金 錐柄麻花鉆 直徑系列為 d=6.8mm,因而對于48M螺紋孔鉆孔時選擇直徑 d=6.8mm 硬質合金 錐柄麻花鉆 。由于被加工材料為合金鑄鋁, 由切削用量簡明手冊第 46 頁表 2.2
29、 知鉆頭幾何參數(shù)分別為,取為;290 140118 攻絲: 由于在之前的工序已經將 4 孔徑鉆至 6.8mm,則根據(jù)直徑參數(shù)選擇對應的絲錐進行攻絲加工。銑銑128.8mm凸凸臺臺表表面面 :機床仍然為上述相同的加工中心 。機械畢業(yè)設計8因銑削寬度=128mm180mm,由切削用量簡明手冊 第 84 頁表 3.1 和機械ae制造工藝設計簡明手冊 第 100 頁表 3.1-28 知應選用直徑 d=200250mm 的硬質合金鑲齒套式面銑刀。 已知總余量為 3mm,則銑削深度6mm,銑削寬度=128mm260mm,查切削用ae量簡明手冊 第 84 頁表 3.1 和切削用量簡明手冊 第 96 頁表 3
30、.16 知選用=200mm 的硬質合金端銑刀。由于 合金鑄鋁 硬度 40110HBS,小于 220HBS,因而由0d切削用量簡明手冊 第 6 頁表 1.2 選擇硬質合金牌號為 YG6 的硬質合金刀片,由切削用量簡明手冊 第 96 頁表 3.16 知齒數(shù)為 16;查切削用量簡明手冊 第 84 頁表 3.2,由于合金鑄鋁 硬度 110HBS150HBS,而銑削余量較小,則銑刀主偏角,過渡刃偏角,副偏角,45kr30kr5kr,0801020s 015鏜鏜56mm孔孔、鏜鏜50.4mm孔孔:機床仍然為上述相同的加工中心, 已知各孔 加工單邊總余量為 2mm,由機械加工工藝師手冊第 3-284 頁表
31、3.3-41 知選用機夾單刃鏜刀,由于最小鏜孔直徑為D=56mm63mm,故選擇的鏜刀各參數(shù)分別為桿部直徑d=50mm,總長 L=350mm,尺寸00.2535fmm.鏜鏜65.8mm孔孔及及56mm與與65.8mm所所成成的的臺臺階階面面:機床仍然為上述相同的加工中心,65.8mm孔加工單邊總余量為 2mm,在鏜削65.8mm孔的同時56mm與65.8mm所成的臺階面的尺寸及粗糙度即可得到保證。由機械加工工藝師手冊第 3-284 頁表 3.3-41 知選用機夾單刃鏜刀,由于最小鏜孔直徑為 D=65.8mm80mm,故選擇的鏜刀各參數(shù)分別為桿部直徑d=60mm,總長 L=400mm,尺寸00.
32、2545fmm.鉆鉆并并攻攻絲絲410M螺螺紋紋孔孔: 由于各孔徑均小于 1520mm,故查機械制造工藝設計簡明手冊 第 20 頁表1.4-7 知只需要經過鉆孔、攻絲即可。鉆孔:由 機械制造工藝設計簡明手冊 第 70 頁表 2.3-20 知 M10 螺紋孔攻絲前鉆孔用麻花鉆鉆頭 直徑有為 8.5mm,由機械制造工藝設計簡明手冊 第 84 頁表3.1-6 知選用硬質合金 錐柄麻花鉆 直徑系列為 d=8.5mm。由于被加工材料為合金鑄鋁,由切削用量簡明手冊 第 46 頁表 2.2 知鉆頭幾何參數(shù)分別為,取為290 140 9;118攻絲: 對410M螺紋孔在此道工序即進行攻絲加工, 由于在之前已經
33、將待加工410M螺紋孔孔徑鉆至 8.5mm,則可根據(jù)相應的直徑參數(shù)選擇對應的絲錐進行攻絲加工。銑銑削削內內部部三三凸凸耳耳下下表表面面 :機床仍然為上述相同的加工中心, 銑削寬度=28.4mm,由機械制造工藝設計ae簡明手冊 第 102 頁表 3.1-31 知應選用直徑 D=40mm 的 7:24 錐柄立銑刀。專用夾具及游標卡尺。 已知總余量為 2.5mm 即為銑削深度 ,銑削寬度=28.4mm,銑削材料為合金鑄鋁,ae硬度偏小, 查切削用量簡明手冊 第 84 頁表 3.1 知選用=40mm 的高速鋼立 銑刀0d即可滿足要求 。由機械制造工藝設計簡明手冊 第 102 頁表 3.1-31 知齒數(shù)
34、為 8; 查切削用量簡明手冊 第 84 頁表 3.2,由于合金鑄鋁 硬度40110HBS150HBS,而銑削余量較小,則 所選擇的 7:24 錐柄高速鋼立 銑刀刀齒螺旋角,后角,前角20016015鏜鏜72.8mm內內圓圓表表面面及及50.4mm與與72.8mm所所成成的的臺臺階階面面 :機床仍然為上述相同的加工中心, 已知加工單邊總余量為 2mm,由機械加工工藝師手冊第 3-284 頁表 3.3-41 知可選用機夾單刃鏜刀,由于最小鏜孔直徑為D=72.8mm80mm,故選擇的鏜刀各參數(shù)分別為桿部直徑d=20mm,總長 L=150mm.銑銑削削12 10mm 矩矩形形槽槽:機床仍然為上述相同的
35、加工中心, 銑削寬度=12mm,銑削高度 h=10mm,由機ae械制造工藝設計簡明手冊 第 101 頁表 3.1-30 知粗銑時選用直徑11dmm的莫氏錐柄立銑刀,標準92Lmm,22lmm,選擇中齒,齒數(shù)為 4,由機械制造工藝設計簡明手冊 第 101 頁表 3.1-30 知半精銑時 選用直徑12dmm的莫氏錐柄立 銑刀,標準96Lmm,26lmm,選擇細齒,齒數(shù)為 5。銑銑削削126mm與與77mm形形成成的的凸凸臺臺表表面面:機床仍然為上述相同的加工中心 。因銑削寬度=126mm180mm,由切削用量ae簡明手冊 第 84 頁表 3.1 和機械制造工藝設計簡明手冊 第 100 頁表 3.1
36、-28 知應選用直徑 d=200250mm 的硬質合金鑲齒套式面銑刀。 機械畢業(yè)設計10已知加工 總余量為 3mm,銑削深度6mm,銑削寬度=126mm180mm,查切削ae用量簡明手冊 第 84 頁表 3.1 和切削用量簡明手冊 第 96 頁表 3.16 知選用=200mm 的硬質合金端銑刀。由于 合金鑄鋁 硬度 40110HBS,小于 220HBS,因而由0d切削用量簡明手冊 第 6 頁表 1.2 選擇硬質合金牌號為 YG6 的硬質合金刀片,由切削用量簡明手冊 第 96 頁表 3.16 知齒數(shù)為 16; 查切削用量簡明手冊 第 84 頁表 3.2,由于合金鑄鋁 硬度 110HBS150HB
37、S,而銑削余量較小,則銑刀主偏角,過渡刃偏角,副偏角,45kr30kr5kr,0801020s 015鏜鏜77mm孔孔:機床仍然為上述相同的加工中心, 已知加工單邊總余量為 2mm,由機械加工工藝師手冊第 3-284 頁表 3.3-41 知可選用機夾單刃鏜刀,由于最小鏜孔直徑為D=77mm80mm,故選擇的鏜刀各參數(shù)分別為桿部直徑d=20mm,總長 L=150mm.鉆鉆并并攻攻絲絲126mm凸凸臺臺上上410M螺螺紋紋孔孔: 由于各孔徑均小于 1520mm,故查機械制造工藝設計簡明手冊 第 20 頁表1.4-7 知對于各孔只需要經過鉆孔后即可攻絲,經濟精度為IT810 級。鉆孔:由 機械制造工
38、藝設計簡明手冊 第 70 頁表 2.3-20 知 M10 螺紋孔攻絲前鉆孔用麻花鉆鉆頭 直徑有為 8.5mm,由機械制造工藝設計簡明手冊 第 84 頁表3.1-6 知硬質合金 錐柄麻花鉆 直徑系列為 d=8.5mm。由于被加工材料為合金鑄鋁, 由切削用量簡明手冊 第 46 頁表 2.2 知鉆頭幾何參數(shù)分別為,取為;290 140118 攻絲: 由于在之前的工序已經將 4 孔徑鉆至 8.5mm,則根據(jù)直徑參數(shù)選擇對應的絲錐進行攻絲加工。攻攻絲絲 8-M8 螺螺紋紋孔孔: 由于在之前的工序已經將作為精基準的2 孔徑鉆、鉸至 6.8mm,不作為精基準的6 孔也鉆至 6.8mm,則根據(jù)相應的直徑參數(shù)選
39、擇對應的絲錐進行攻絲加工。 113 3. .4 4. .加加工工工工序序設設計計一、 機械加工余量的確定銑銑削削下下底底面面 : 由機械制造工藝設計簡明手冊 第 74 頁加工余量表 2.321 可得雖然下底面表面粗糙度要求僅 12.5,但要作為精基準,故表面粗糙度至少需要達到3.2,需進行粗銑、半精銑、精銑三次銑削, 總余量為 5mm,粗銑時銑削深度=3mm,半精銑時銑ap削深度=1.5mm,精銑時銑削深度=0.5mm;apap加加工工下下底底面面作作為為精精基基準準的的 2 2- -M M8 8 螺螺紋紋孔孔: 雖然該螺紋孔無特殊加工要求,但由于要作為精基準,故攻絲前孔的內表面粗糙度要求至少
40、為 3.2,而孔徑15 20mm,由機械制造工藝設計簡明手冊 第 20 頁表1.4-7 知需經過鉆、鉸可滿足要求。在上面工藝路線的設定中已查得鉆頭相關參數(shù),M8 螺紋孔攻絲前孔徑尺寸須為6.8mm,故作為精基準的兩孔在鉆孔時需選擇直徑系列小一級的 6.5mm 鉆頭,為鉸孔留下 0.3mm 的余量。銑銑削削86.8mm凸凸臺臺表表面面: 該表面粗糙度要求為 2.5,由機械制造工藝設計簡明手冊 第 21 頁表 1.4-8知需進行粗銑、半精銑、精銑才可達到要求,由機械制造工藝設計簡明手冊 第39 頁表 2.2-4 知加工總余量為 2.5mm,粗銑時銑削深度=1.5mm,半精銑時銑削深ap度=0.5m
41、m,精銑時銑削深度=0.5mm.apap粗粗銑銑420mm所所在在凸凸臺臺表表面面: 該表面無粗糙度要求 ,由機械制造工藝設計簡明手冊 第 21 頁表 1.4-8 知只需進行粗銑, 由機械制造工藝設計簡明手冊 第 39 頁表 2.2-4 知總余量為2.5mm,將毛坯余量一次銑削完畢即可 。銑銑128.8mm凸凸臺臺表表面面 : 表面粗糙度要求為 6.3,由機械制造工藝設計簡明手冊 第 21 頁表 1.4-8 知只需進行粗銑、精銑即可達到要求, 由機械制造工藝設計簡明手冊 第 39 頁表2.2-4 知加工總余量為 3mm,粗銑時銑削深度=2.5mm,精銑時銑削深度=0.5mm.apap鏜鏜56m
42、m孔孔、鏜鏜50.4mm孔孔: 56mm孔以及50.4mm孔內圓柱面粗糙度要求均為 12.5,由機械制造工藝設計簡明手冊 第 39 頁表 2.2-4 知加工單邊總余量為 2mm,由機械制造工藝設計簡明手冊第 21 頁表 1.4-7 知只需經過粗鏜即可滿足粗糙度要求,粗鏜深度2mm.鏜鏜65.8mm孔孔及及56mm與與65.8mm所所成成的的臺臺階階面面: 65.8mm孔內圓柱 面粗糙度要求為 3.2,由機械制造工藝設計簡明手冊 第 39機械畢業(yè)設計12頁表 2.2-4 知加工單邊總余量為 2mm,由機械制造工藝設計簡明手冊 第 20 頁表1.4-7 知需經過粗鏜和半精鏜可達到要求, 粗鏜65.
43、8mm內圓柱面深度 1.5mm,半精鏜深度 0.5mm,在鏜削65.8mm孔的同時只需控制鏜刀的橫向進給位置56mm與65.8mm所成的臺階面的尺寸及粗糙度即可得到保證,56mm與65.8mm所成的臺階面余量為 2.5mm.銑銑削削內內部部三三個個凸凸耳耳下下表表面面 : 表面粗糙度要求為僅 6.3,由機械制造工藝設計簡明手冊 第 21 頁表 1.4-8知只需進行粗銑和精銑即可達到要求, 由機械制造工藝設計簡明手冊 第 39 頁表2.2-4 知總余量為 2.5mm,粗銑時銑削深度=2mm,精銑時銑削深度=0.5mm;apap鏜鏜72.8mm內內圓圓表表面面及及50.4mm與與72.8mm所所成
44、成的的臺臺階階面面 : 表面粗糙度要求為 6.3,由機械制造工藝設計簡明手冊 第 20 頁表 1.4-7 知需經過粗鏜和半精鏜即可滿足要求, 由機械制造工藝設計簡明手冊 第 39 頁表2.2-4 知加工單邊總余量為 2mm,粗鏜72.8mm內圓柱面深度 1.5mm,半精鏜深度0.5mm.銑銑削削12 10mm 矩矩形形槽槽: 表面粗糙度要求為6.3 m,由機械制造工藝設計簡明手冊 第 21 頁表 1.4-8 知只需要經過粗銑和半精銑即可達到要求,粗銑為半精銑預留1mm 余量即可。銑銑削削126mm凸凸臺臺表表面面:該表面粗糙度要求為 6.3,由機械制造工藝設計簡明手冊 第 21 頁表 1.4-
45、8 知只需進行粗銑、精銑即可達到要求, 由機械制造工藝設計簡明手冊 第 39 頁表2.2-4 知加工總余量為 3mm,粗銑時銑削深度=2.5mm,精銑時銑削深度=0.5mm.apap鏜鏜77mm孔孔:孔的內表面粗糙度要求為 6.3,由機械制造工藝設計簡明手冊 第 20 頁表1.4-7 知需經過粗鏜和半精鏜即可滿足要求, 由機械制造工藝設計簡明手冊 第 39頁表 2.2-4 知加工單邊總余量為 2mm,粗鏜77mm內圓柱面深度 1.5mm,半精鏜深度0.5mm.二、 確定切削用量及基本工時 粗粗銑銑、半半精精銑銑、精精銑銑 下下底底面面: 查切削用量簡明手冊 第 88 頁表 3.5 得每齒進給量
46、為 0.180.28mm/z,fz粗銑時取,半精銑和精銑時取,由切削用量簡明手冊 0.28/mm zfz0.18/mm zfz 13第 96 頁表 3.16 知切削速度,主軸轉速66 / minnr,進給速度65/ mincmv,計算實際轉速為229/ minfmmv10001000 65345 / min60cswvrnd由機械制造工藝設計簡明手冊 第 160 頁表 4.2-36 知(加工中心按立式 X52K 銑床)轉速 300r/min,計算實際切削速度為80 30075.36/ min1.26/10001000wwd nvmm s校驗機床功率根據(jù)切削用量簡明手冊 第 105 頁表 3.2
47、4 知合金鑄鋁 硬度在 40110HBS 之間,銑削寬度,粗銑銑削深度,銑刀每齒進給量,每分30mmae3mmap0.28/mm zfz鐘進給量,查得近似功率,而加工中心的銑削加工按功率為229/ minmmvf5.5kwpc15KW 的立式銑床來看,機床主軸允許的功率為,故15 0.7511.25kWPcM,因此所選擇的切削用量可以采用。5.511.25kwkwpPcMc選擇銑刀磨鈍標準和刀具壽命查切削用量簡明手冊 第 89 頁表 3.7 得銑刀刀齒后刀面最大磨損量為1.5,而銑刀直徑,查切削用量簡明手冊 第 89 頁表 3.8 得銑刀壽命 T=180min。080mmd切削工時由機械制造工
48、藝設計簡明手冊 第 198 頁表 6.2-7 公式計算: (1)12lllTjfMz0(0.03 0.05)0.04 803.2dmmc1000.5()(1 3)0.5 803.2 (803.2)226.32ddmmlcc,為銑削輪廓長度 約為 1210mm3 532mmll機床工作臺進給量 0.28 10 300840mm/ minZffnwMzz查機械制造工藝設計簡明手冊 第 161 頁表 4.2-37 取工作臺進給量為 786mm/min則 12121026.3231.6min786jlllTfMz半精銑時 銑削深度,銑刀每齒進給量,則機床工作臺進給量1.5mmap0.18/mm zfz
49、 0.18 10 300540mm/ minZffnwMzz查機械制造工藝設計簡明手冊 第 161 頁表 4.2-37 取工作臺進給量為 500mm/min機械畢業(yè)設計14則 12121026.3232.5min500jlllTfMz精銑時銑削深度,銑刀每齒進給量,則機床工作臺進給量0.5mmap0.18/mm zfz 0.18 10 300540mm/ minZffnwMzz查機械制造工藝設計簡明手冊 第 161 頁表 4.2-37 取工作臺進給量為 500mm/min則 12121020.2432.5min500jlllTfMz則機動工時為 1.6+2.5+2.5=6.6min鉆鉆68孔孔
50、、鉆鉆并并鉸鉸28孔孔、鉆鉆7mm孔孔、鉆鉆并并攻攻絲絲 3 3- -M M1 12 2 螺螺紋紋孔孔: 鉆孔:由切削用量簡明手冊 第 50 頁表 2.7 知當鋁合金硬度200HBS,進給量0.36 0.44/fmm r,由于本零件在鉆各孔時屬于中等剛性零件,故進給量應乘以系數(shù) 0.75,則 (0.36 0.44) 0.750.27 0.33/fmm r 取0.30/fmm r根據(jù)切削用量簡明手冊 第 55 頁表 2.13 查得切削速度9/ minvm,所以鉆88孔時 10001000 9358.1 / min8swvrnd鉆312孔時 10001000 9238.9 / min12swvrn
51、d根據(jù)機床說明書,取300 / minwrn,故實際切削速度為鉆7mm孔時 7 3006.6/ min10001000wwd nvm 鉆88孔時 8 3007.5/ min10001000wwd nvm 鉆312孔時 12 30011.3/ min10001000wwd nvm 15切削工時(鉆一個7mm孔) 1210930.15min300 0.5jwlllTfn切削工時(鉆一個8mm孔) 1221 930.22min300 0.5jwlllTfn切削工時(鉆一個12mm孔) 1210930.15min300 0.5jwlllTfn鉆一個孔時,1210,9,3lmmmmmmll故本工序鉆孔機
52、動工時為0.150.22 80.15 32.36min 由切削用量簡明手冊 第 54 頁表 2.12 查得鉆頭磨鈍限度為 0.40.8mm,7mm孔和鉆88孔時,刀具壽命為 35min,鉆312孔時,刀具壽命為 60min.鉸孔:由于所加工的兩個作為精基準的孔為盲孔,由切削用量簡明手冊 第53 頁表 2.11 查得鉸刀進給量為 0.20.5mm/r,取為 0.5mm/r,由切削用量簡明手冊第 66 頁表 2.24 查得切削速度10 14/ mincmv,根據(jù)機床說明書,取300 / minwrn實際切削速度為8 3007.5/ min10001000wwd nvm 切削工時(一個孔):1221
53、,9,3lmmmmmmll 1221 930.22min300 0.5jwlllTfn鉸 2 個孔時的機動工時為0.22 20.44mint 攻絲312孔時:查詢切削用量手冊可知切削用量為0.1/6/ minvm sm,則轉速為 10001000 6159 / min12swvrnd 按機床選取195 / minwrn,則 12 1957.4/ min0.12/10001000wwd nvmm s攻絲單個孔時,1210,9,3lmmmmmmll 則攻絲單個孔的機動工時 1210930.12min195 1jwlllTfn機械畢業(yè)設計16則攻絲312孔的機動工時0.12 30.36mint 銑銑
54、削削86.8mm凸凸臺臺表表面面: 查切削用量簡明手冊 第 88 頁表 3.5 得每齒進給量為 0.180.28mm/z,fz粗銑時取,半精銑和精銑時取,由切削用量簡明手冊 0.20/mm zfz0.18/mm zfz第 96 頁表 3.16 知切削速度,主軸轉速250 / minnr,進給速度98/ mincmv,計算實際轉速為471/ minfmmv10001000 98249.6 / min125cswvrnd由機械制造工藝設計簡明手冊 第 160 頁表 4.2-36 知(加工中心按立式 X52K 銑床)轉速 300r/min,計算實際切削速度為125 300117.8/ min1.96
55、/10001000wwd nvmm s校驗機床功率合金鑄鋁 硬度在 40110HBS 之間,銑削寬度,粗銑時銑削深度86.8mmae,半精銑時銑削深度,精銑時銑削深度,粗銑時 銑1.5mmap0.5mmap0.5mmap刀每齒進給量,每分鐘進給量,根據(jù)切削用量簡明手0.20/mm zfz471/ minmmvf冊第 105 頁表 3.24 可查得近似功率,而加工中心的銑削加工按功率為1.9kwpc15KW 的立式銑床來看,機床主軸允許的功率為,故15 0.7511.25kWPcM,因此所選擇的切削用量可以采用。1.911.25kwkwpPcMc選擇銑刀磨鈍標準和刀具壽命查切削用量簡明手冊 第
56、89 頁表 3.7 得銑刀刀齒后刀面最大磨損量為1.5,而銑刀直徑=125mm,查切削用量簡明手冊 第 89 頁表 3.8 得銑刀壽命 T=180min。0d切削工時由機械制造工藝設計簡明手冊 第 198 頁表 6.2-7 公式計算: 12jlllTfMz0(0.03 0.05)0.04 1255dmmc1000.5()(1 3)0.5 1255 (1255)240.0ddmmlcc,為銑削輪廓長度 86.8mm23 53mmll粗銑時機床工作臺進給量0.20 12 300720mm/ minwzZffnMz查機械制造工藝設計簡明手冊 第 161 頁表 4.2-37 取工作臺進給量為 600m
57、m/min 17則粗銑時 1286.840.030.22min600jlllTfMz半精銑時,則機床工作臺進給量0.18/mm zfz0.18 12 300648mm/ minwzZffnMz查機械制造工藝設計簡明手冊 第 161 頁表 4.2-37 取工作臺進給量為 300mm/min則 1286.840.030.44min300jlllTfMz精銑時,則機床工作臺進給量0.18/mm zfz0.18 12 300648mm/ minwzZffnMz查機械制造工藝設計簡明手冊 第 161 頁表 4.2-37 取工作臺進給量為 300mm/min則 1286.840.030.44min300j
58、lllTfMz則機動工時為 0.22+0.44+0.44=1.1min粗粗銑銑420mm所所在在凸凸臺臺表表面面: 查切削用量簡明手冊 第 88 頁表 3.5 得每齒進給量為 0.180.28mm/z,取fz,由切削用量簡明手冊 第 96 頁表 3.16 知切削速度,0.18/mm zfz110/ mincmv主軸轉速439 / minnr,進給速度,計算實際轉速為492/ minmmvf10001000 110436.5 / min80cswvrnd由機械制造工藝設計簡明手冊 第 160 頁表 4.2-36 知(加工中心按立式 X52K 銑床)轉速 300r/min,計算實際切削速度為80
59、30075.4/ min1.26/10001000wwd nvmm s校驗機床功率合金鑄鋁 硬度在 40110HBS 之間,銑削寬度,只經一次粗銑, 粗銑時20mmae銑削深度,銑刀每齒進給量,每分鐘進給量2.5mmap0.18/mm zfz,根據(jù)切削用量簡明手冊 第 105 頁表 3.24 可查得近似功率492/ minmmvf,而加工中心的銑削加工按功率為15KW 的立式銑床來看,機床主軸允許的1.3kwpc功率為,故,因此所選擇的切削用15 0.7511.25kWPcM1.311.25kwkwpPcMc機械畢業(yè)設計18量可以采用。選擇銑刀磨鈍標準和刀具壽命查切削用量簡明手冊 第 89 頁
60、表 3.7 得銑刀刀齒后刀面最大磨損量為1.5,而銑刀直徑=80mm,查切削用量簡明手冊 第 89 頁表 3.8 得銑刀壽命 T=180min。0d切削工時由機械制造工藝設計簡明手冊 第 198 頁表 6.2-7 公式計算: 12jlllTfMz0(0.03 0.05)0.04 803.2dmmc1000.5()(1 3)0.5 803.2 (803.2)226.3ddmmlcc,為銑削輪廓長度 20mm23 53mmll機床工作臺進給量0.18 10 300540mm/ minwzZffnMz查機械制造工藝設計簡明手冊 第 161 頁表 4.2-37 取工作臺進給量為 320mm/min則
61、122026.330.16min320jlllTfMz機動工時為4 0.160.64min鉆鉆并并攻攻絲絲420mm凸凸臺臺上上的的48M螺螺紋紋孔孔: 鉆孔:由切削用量簡明手冊 第 50 頁表 2.7 知進給量0.47 0.57/fmm r,由于本零件鉆孔所在零件屬于中等剛性零件,故進給量應乘以系數(shù)0.75,則 (0.47 0.57) 0.750.35 0.43/fmm r根據(jù)機械制造工藝設計簡明手冊 第 168 頁表 4.2-47 知取進給量為0.316/fmm r,由切削用量簡明手冊 第 57 頁表 2.15 知切削速度,23/ minmvc,機械制造工藝設計簡明手冊 第 168 頁表1
62、0001000 23915.6 / min8swvrnd4.2-47 知鉆軸轉速取為 634r/min,故實際切削速度8 63415.9/ min0.27/10001000wwd nvmm s 切削工時 18(1 2)14 0.6 13.4mm5922Dctgctgl 21 42mml 19 為走刀長度為 21mml 工作臺進給量0.316 634200.4mm/ minfnfn則 1221 3.420.13min200.4jlllTfn則鉆孔的機動工時為4 0.130.52min 攻絲:查詢切削用量手冊可知切削用量為0.1/6/ minvm sm,則轉速為 10001000 6238 / m
63、in8swvrnd 按機床選取195 / minwrn,則 8 1954.9/ min10001000wwd nvm 攻絲單個孔時,1219,3,3lmmmmmmll 則攻絲的機動工時 1(1933) 241.02min195 1mt 銑銑128.8mm凸凸臺臺表表面面 : 查切削用量簡明手冊 第 88 頁表 3.5 得每齒進給量為 0.180.28mm,粗fz銑時取,精銑時,由切削用量簡明手冊 第 96 頁表0.20/mm zfz0.18/mm zfz3.16 知切削速度,主軸轉速142 / minnr,進給速度,89/ minmvc358/ minmmvf計算實際轉速為10001000 8
64、9141.6 / min200cswvrnd由機械制造工藝設計簡明手冊 第 160 頁表 4.2-36 知(加工中心按立式 X52K 銑床)轉速 300r/min,計算實際切削速度為200 300188.4/ min3.14/10001000wwd nvmm s校驗機床功率合金鑄鋁 硬度在 40110HBS 之間,銑削寬度,粗銑銑削深度128.8mmae,銑刀每齒進給量,每分鐘進給量,根據(jù)3mmap0.18/mm zfz358/ minmmvf切削用量簡明手冊 第 105 頁表 3.24 可查得近似功率,而加工中心的銑3.3kwpc削加工按功率為 15KW 的立式銑床來看,機床主軸允許的功率為
65、,故,因此所選擇的切削用量可以15 0.7511.25kWPcM3.311.25kwkwpPcMc采用。選擇銑刀磨鈍標準和刀具壽命機械畢業(yè)設計20查切削用量簡明手冊 第 89 頁表 3.7 得銑刀刀齒后刀面最大磨損量為1.5,而銑刀直徑=200mm,查切削用量簡明手冊 第 89 頁表 3.8 得銑刀壽命 T=240min。0d切削工時由機械制造工藝設計簡明手冊 第 198 頁表 6.2-7 公式計算: 12jlllTfMz0(0.03 0.05)0.04 2008dmmc1000.5()(1 3)0.5 2008 (2008)262.8ddmmlcc,為銑削輪廓長度 128.8mm23 53m
66、mll機床工作臺進給量0.20 16 300960mm/ minwzZffnMz查機械制造工藝設計簡明手冊 第 161 頁表 4.2-37 取工作臺進給量為 600mm/min則 12128.862.830.33min600jlllTfMz精銑時,則機床工作臺進給量0.18/mm zfz0.18 16 300864mm/ minwzZffnMz查機械制造工藝設計簡明手冊 第 161 頁表 4.2-37 取工作臺進給量為 320mm/min則 12128.862.830.61min320jlllTfMz則機動工時為 0.33+0.61=0.94min鏜鏜50.4mm孔孔:查切削用量簡明手冊 第 11 頁表 1.5 得進給量為0.30.4/mm r,取f=0.3mm/r,根據(jù)相關手冊確定鏜削的切削速度,計算實際f100/ min1.67/mm svc轉速為10001000 100631.5 / min50.4cwwvrnd查機械制造工藝設計簡明手冊 第 153 頁表 4.2-26 選擇轉速為 625r/min.由機械制造工藝設計簡明手冊 第 193 頁表 6.2-1 知鏜孔切削工時 12j
- 溫馨提示:
1: 本站所有資源如無特殊說明,都需要本地電腦安裝OFFICE2007和PDF閱讀器。圖紙軟件為CAD,CAXA,PROE,UG,SolidWorks等.壓縮文件請下載最新的WinRAR軟件解壓。
2: 本站的文檔不包含任何第三方提供的附件圖紙等,如果需要附件,請聯(lián)系上傳者。文件的所有權益歸上傳用戶所有。
3.本站RAR壓縮包中若帶圖紙,網(wǎng)頁內容里面會有圖紙預覽,若沒有圖紙預覽就沒有圖紙。
4. 未經權益所有人同意不得將文件中的內容挪作商業(yè)或盈利用途。
5. 裝配圖網(wǎng)僅提供信息存儲空間,僅對用戶上傳內容的表現(xiàn)方式做保護處理,對用戶上傳分享的文檔內容本身不做任何修改或編輯,并不能對任何下載內容負責。
6. 下載文件中如有侵權或不適當內容,請與我們聯(lián)系,我們立即糾正。
7. 本站不保證下載資源的準確性、安全性和完整性, 同時也不承擔用戶因使用這些下載資源對自己和他人造成任何形式的傷害或損失。