中型普通車床主軸變速箱設計
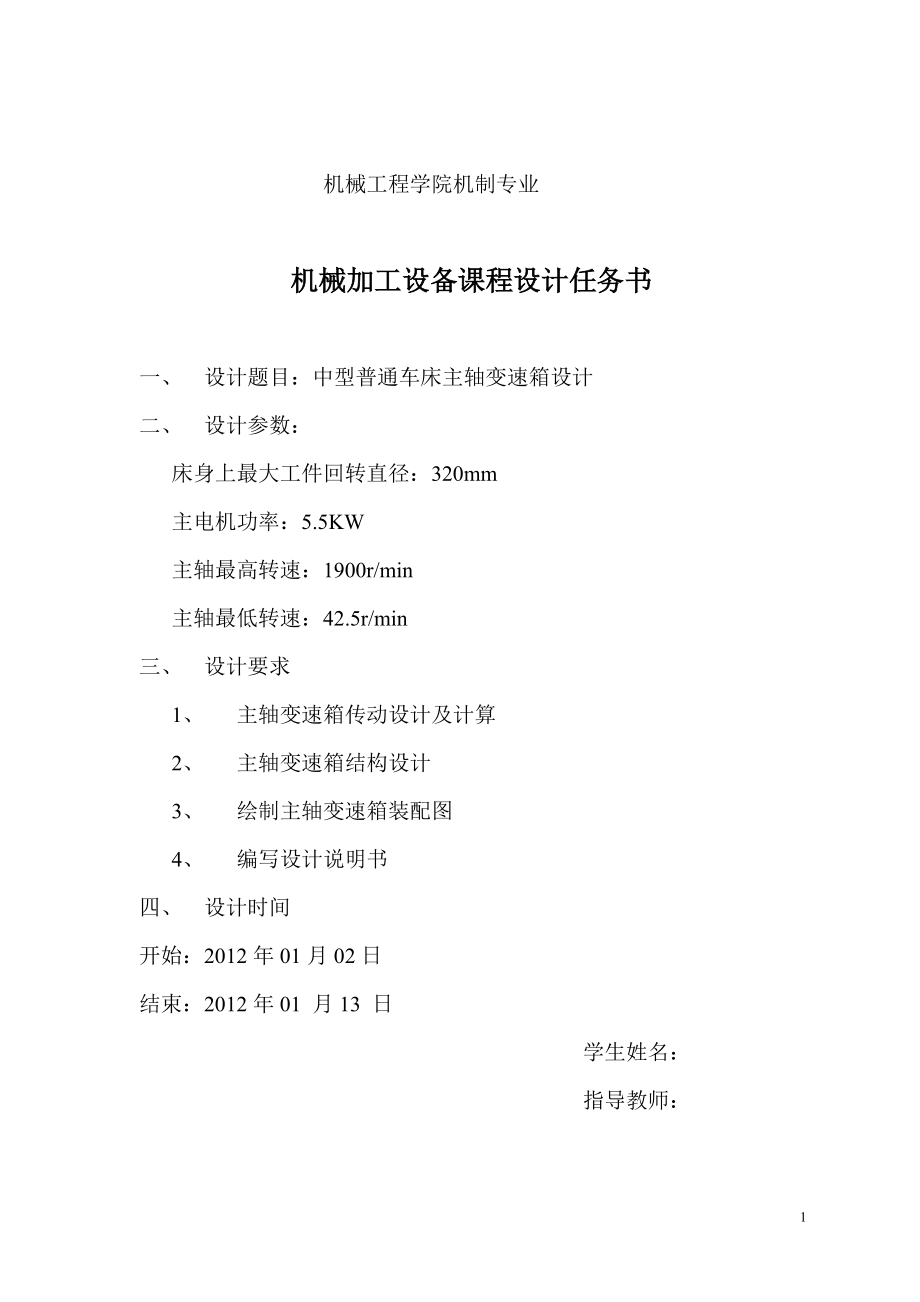


《中型普通車床主軸變速箱設計》由會員分享,可在線閱讀,更多相關《中型普通車床主軸變速箱設計(30頁珍藏版)》請在裝配圖網(wǎng)上搜索。
1、 機械工程學院機制專業(yè) 機械加工設備課程設計任務書 一、 設計題目:中型普通車床主軸變速箱設計 二、 設計參數(shù): 床身上最大工件回轉直徑:320mm 主電機功率:5.5KW 主軸最高轉速:1900r/min 主軸最低轉速:42.5r/min 三、 設計要求 1、 主軸變速箱傳動設計及計算 2、 主軸變速箱結構設計 3、 繪制主軸變速箱裝配圖 4、 編寫設計說明書 四、 設計時間 開始:2012年01月02日 結束:2012年01 月13 日 學生姓名:
2、 指導教師: 一、傳動設計 1.1電機的選擇 (1)床身上最大回轉直徑:320mm (2)主電機功率:5.5KW (3)主軸最高轉速:1900r/min 參考《機床主軸變速箱設計指導》(以下簡稱《設計指導》)P16選擇Y132S-4型三相異步電動機。 1.2運動參數(shù) 變速范圍 Rn==1900/42.5=44.7= 對于中型車床,=1.26或=1.41 此處?。?.41 得轉速級數(shù)Z=12。查《設計指導》P6
3、標準數(shù)列表得轉速系列為:42.5、60、85、118、170、236、335、475、670、950、1320、1900。 1.3擬定結構式 1.3.1 確定變速組傳動副數(shù)目 實現(xiàn)12級主軸轉速變化的傳動系統(tǒng)可以寫成多種傳動副組合: 12=34 12=43 12=322 12=232 12=223 在上列兩行方案中,第一行的方案有時可以節(jié)省一根傳動軸,缺點是有一個傳動組內(nèi)有四個傳動副。如用一個四聯(lián)滑移齒輪,則會增加軸向尺寸;如果用兩個雙聯(lián)滑移齒輪,操縱機構必須互鎖以防止兩個雙聯(lián)滑移齒輪同時嚙合,所以少用。 根據(jù)傳動副數(shù)目分配應“前多后少”的原則,方案12=
4、322是可取的。但是,由于主軸換向采用雙向離合器結構,致使Ⅰ軸尺寸加大,此方案也不宜采用,而應選用方案12=232。 1.3.2確定變速組擴大順序 12=232的傳動副組合,其傳動組的擴大順序又可以有以下6種形式: A、12=213226 B、12=213422 C、12 =233126 D、12=263123 E、12=223421 F、12=263221 根據(jù)級比指數(shù)要“前疏后密”的原則,應選用方案A。然而,然而,對于所設計的機構,將會出現(xiàn)兩個問題: ① 第一變速組采用降速傳動(圖
5、a)時,由于摩擦離合器徑向結構尺寸限制,在結構上要求有一齒輪的齒根圓大于離合器的直徑,使得Ⅰ軸上的齒輪直徑不能太小,Ⅱ軸上的齒輪則會成倍增大。這樣,不僅使Ⅰ-Ⅱ軸間中心距加大,而且Ⅱ-Ⅲ軸間的中心距也會加大,從而使整個傳動系統(tǒng)結構尺寸增大。這種傳動不宜采用。 ② 如果第一變速組采用升速傳動(圖b),則Ⅰ軸至主軸間的降速傳動只能由后兩個變速組承擔。為了避免出現(xiàn)降速比小于允許的極限值,常常需要增加一個定比降速傳動組,使系統(tǒng)結構復雜。這種傳動也不是理想的。 如果采用方案C、12 =233126(圖c) 則可解決上述存在的問題。 其結構網(wǎng)如下圖所示: 1.4擬定轉速圖 1.4.1
6、驗算傳動組變速范圍 第二擴大組的變速范圍R2==8,符合設計原則要求,方案可用。 由第二擴大組的變速范圍R2==8= 可知第二擴大組兩個傳動副的傳動必然是傳動比的極限值。所以轉速圖擬定如下: 1.5確定齒輪齒數(shù) 查《金屬切削機床》表8-1各種傳動比的適用齒數(shù)求出各傳動組齒輪齒數(shù)如下表: 變速組 第一變速組a 第二變速組b 第三變速組c 齒數(shù)和 72 72 90 齒輪 Z1 齒數(shù) 24 48 42 30 19 53 24 48 30 42 60 30 18 72 傳動過程中,會采用
7、三聯(lián)滑移齒輪,為避免齒輪滑移中的干涉,三聯(lián)滑移齒輪中最大和次大齒輪之間的齒數(shù)差應大于4。所選齒輪的齒數(shù)符合設計要求。 1.6確定帶輪直徑 1.6.1確定計算功率Pca 由《機械設計》表8-7查得工作情況系數(shù)=1.1故 Pca =P=1.15.5=6.05KW 1.6.2選擇V帶類型 據(jù)Pca、的值由《機械設計》圖8-11選擇A型帶。 1.6.3確定帶輪直徑并驗算帶速V 由《機械設計》表8-6、表8-8,取基準直徑=100mm。 驗算帶速V V =π/(601000)=π1001440/(601000)=7.54m/s 因為5m/s<V<30m/s,所以
8、帶輪合適。 定大帶輪直徑 =i(1-ε)=(1440/950)125(1-0.02)=148.55mm ε――帶的滑動系數(shù),一般取0.02 據(jù)《機械設計》表8-8,取基準直徑=150mm。 1.7驗算主軸轉速誤差 主軸各級實際轉速值用下式計算: n = nE(1-ε)u1 u2 u3 式中 u1 u2 u3 分別為第一、第二、第三變速組齒輪傳動比; nE 為電機的滿載轉速 ;ε取0.02。 轉速誤差用主軸實際轉速與標準轉速相對誤差的絕對值表示: △ n
9、= | |≤10(Φ-1)%10(1.41-1)%=4.1% 其中主軸理想轉速 把數(shù)據(jù)依次代入公式得出下表 主軸轉速 n1 n2 n3 n4 n5 n6 理想轉速 42.5 60 85 118 170 236 實際轉速 42.16 58.80 84.00 118.04 164.64 235.20 轉速誤差% 0.8 2 1.18 0.03 3.15 0.34 主軸轉速 n7 n8 n9 n10 n11 n12 理想轉速 335 475 670 950 1320 1900 實際轉速 337.27 470
10、.40 672.00 944.35 1317.12 1881.6 轉速誤差% 0.68 0.30.97 0.30 0.59 0.22 0.97 轉速誤差滿足要求,數(shù)據(jù)可用。 1.8繪制傳動系統(tǒng)圖 二、估算主要傳動件,確定其結構尺寸 2.1確定傳動件計算轉速 2.1.1主軸計算轉速 主軸計算轉速是第一個三分之一轉速范圍內(nèi)的最高一級轉速,即 nj = nmin=119.14r/min 即n4=118r/min; 2.1.2各傳動軸計算轉速 軸Ⅲ可從主軸為118r/min按18/72的傳動副找上去,似應為475r/min。但是由于軸Ⅲ上的最低轉速170r/
11、min經(jīng)傳動組c可使主軸得到42.5r/min和335r/min兩種轉速。335r/min要傳遞全部功率,所以軸Ⅲ的計算轉速應為170r/min。軸Ⅱ的計算轉速可按傳動副b推上去,得475r/min。軸Ⅰ的計算轉速為950r/min。 各軸的計算轉速列表如下 軸 Ⅰ Ⅱ Ⅲ Ⅳ 計算轉速nj 950 475 170 118 2.1.3各齒輪計算轉速 齒輪 Z1 齒數(shù) 24 48 42 30 19 53 24 48 30 42 60 30 18 72 nj 950 475 9
12、50 1320 475 170 475 236 475 335 170 335 475 118 2.2初估軸直徑 2.2.1確定主軸支承軸頸直徑 據(jù)電機的功率參考《機械制造工藝金屬切削機床設計指南》(以下簡稱《設計指南》)表2.3-2,取主軸前軸頸直徑D1 = 80mm,后軸頸直徑D2 = (0.7~0.85)D1,取D2 = 60 mm。 2.2.2初估傳動軸直徑 按扭轉剛度初步計算傳動軸直徑 d = 式中d —— 傳動軸危險截面處直徑; N —— 該軸傳遞功率(KW); N=η; η——從電機
13、到該傳動軸間傳動件的傳動效率(不計軸承上的效率),對估算傳動軸直徑影響不大可忽略; ——該軸計算轉速(r/min); []—— 該軸每米長度允許扭轉角 這些軸都是一般傳動軸,據(jù)《設計指導》P32取[]=1deg/m。 根據(jù)傳動系統(tǒng)圖上的傳動件布置情況初步估計各軸長度如下表 軸 Ⅰ Ⅱ Ⅲ Ⅳ 長度 640 600 740 840 對Ⅰ軸 d= ==28mm 對Ⅱ軸 d= ==38mm 對Ⅲ軸 d= ==46mm 考慮到軸是花鍵軸所以軸直徑作為花鍵軸小徑,據(jù)《設計指南》附表2.3-1取d1=32mm,花鍵規(guī)格NdDB(鍵數(shù)小徑大徑鍵
14、寬)=832366;d2=42mm,花鍵規(guī)格NdDB(鍵數(shù)小徑大徑鍵寬)=842468;d3=46mm,花鍵規(guī)格NdDB(鍵數(shù)小徑大徑鍵寬)=846509。 綜上對傳動軸直徑估算結果如下 軸 Ⅰ Ⅱ Ⅲ 直徑 32 42 46 花鍵 832366 842468 846509 2.3估算傳動齒輪模數(shù) 參考《設計指導》P36中齒輪模數(shù)的初步計算公式初定齒輪的模數(shù) 按齒輪彎曲疲勞的估算 mw ≥ 32 mm 按齒面點蝕的估算 A ≥ 370 mm mj = 式中 N
15、 —— 該軸傳遞功率(KW); N=η; η——從電機到該傳動軸間傳動件的傳動效率(不計軸承上的效率); ——大齒輪的計算轉速(r/min); Z —— 所算齒輪的齒數(shù); A——齒輪中心距 同一變速組中的齒輪取同一模數(shù),按工作負荷最重(通常是齒數(shù)最小)的齒輪進行計算,然后取標準模數(shù)值作為該變速組齒輪的模數(shù)。據(jù)《設計指導》P32取每兩傳動軸間傳動件的傳動效率η=0.96 傳動組a中 按齒輪彎曲疲勞的估算 mw ≥ 32 mm = 32 =9.12mm 按齒面點蝕的估算 A ≥ 370 mm=370=82.57mm
16、 mj= mm= =2.29mm 取標準模數(shù)m=3mm 傳動組b中 按齒輪彎曲疲勞的估算 mw≥ 32 mm = 32 =2.65mm 按齒面點蝕的估算 A ≥ 370 mm=370=115.13mm mj= mm= =3.20mm 取標準模數(shù)m=4mm 傳動組c中 按齒輪彎曲疲勞的估算 mw ≥ 32 mm = 32 =2.68 mm 按齒面點蝕的估算 A ≥ 370 mm=370=129.16mm
17、 mj= mm= =2.87 取標準模數(shù)m=3mm 2.4片式摩擦離合器的選擇及計算 2.4.1決定外摩擦片的內(nèi)徑 結構為軸裝式,則外摩擦片的內(nèi)徑比安裝軸的軸徑D大2~6 mm有 =D+(2~6)=36+(2~6) =38~42mm 取=42mm 2.4.2選擇摩擦片尺寸 參考《設計指導》P41表摩擦片尺寸及花鍵規(guī)格自行設計摩擦片的尺寸如圖所示 2.4.3計算摩擦面對數(shù)Z Z 式中Mn――額定動扭矩;Mn=9550=9550=80.04Nm K=1.3~1.5;取 K=1.3;
18、 f——摩擦片間的摩擦系數(shù);查《設計指導》表12 f=0.08(摩擦片材料10鋼,油潤) [P]——摩擦片基本許用比壓;查《設計指導》表12 [P]=0.8MPa(摩擦片材料10鋼,油潤); D——摩擦片內(nèi)片外徑 mm; ――外摩擦片的內(nèi)徑mm; ——速度修正系數(shù);根據(jù)平均圓周速度(1.62m/s)查《設計指導》表13近似取為1.2; ——結合次數(shù)修正系數(shù);查《設計指導》表13取為0.84; ――接合面修正系數(shù); 把數(shù)據(jù)代入公式得Z=10.8 查《設計指導》表13取Z=14 2.4.4計算摩擦片片數(shù) 摩擦片總片數(shù)(Z+1)=15片 2.4.5計算軸向壓
19、力Q Q=[p]Kv =0.81.2 =478N 2.5V帶的選擇及計算 2.5.1初定中心距 由前面部分V帶輪直徑的選擇結合公式有 =(0.6~2)(+) =(0.6~2)(100+150) =150~500mm ?。?50mm 2.5.2確定V帶計算長度L及內(nèi)周長 =2+ =+2450 =1294.09mm 據(jù)《設計指導》P30表計算長度取L=1275mm. 2.5.3驗算V帶的撓曲次數(shù) μ=≤40次/s 式中m――帶輪個數(shù); 把數(shù)據(jù)代入上式得μ=8.23≤40次/s,數(shù)據(jù)可用。 2.5.4確定中心距a a=+=+450=440
20、.455mm 取a=440mm 2.5.5驗算小帶輪包角 ≈- =- =≥ 滿足要求。 2.5.6計算單根V帶的額定功率 由=100min和=1440r/min,查《機械設計》表8-4a得=1.32KW; 據(jù)=1440r/min和i=1.50和A型帶,查《機械設計》表8-4b得△=0.13KW; 查《機械設計》表8-5得=0.99; 查《機械設計》表8-2得=0.93; 有 =(+△) =(1.32+0.13)0.990.93 =1.34 2.5.7計算V帶的根數(shù) Z=/=6.05/1.34=
21、4.5 取Z=5根 三、結構設計 3.1帶輪的設計 根據(jù)V帶計算,選用5根A型V帶。由于Ⅰ軸安裝摩擦離合器及傳動齒輪,為了改善它們的工作條件,保證加工精度,采用卸荷式帶輪結構輸入。如圖所示,帶輪支承在軸承外圓上,而兩軸承裝在與箱體固定的法蘭盤上,扭矩從端頭花鍵傳入。 3.2主軸換向機構的設計 主軸換向比較頻繁,才用雙向片式摩擦離合器。這種離合器由內(nèi)摩擦片、外摩擦片、滑動套筒、螺母、鋼球和空套齒輪等組成。離合器左右兩部門結構是相同的。左離合器傳動主軸正轉,用于切削加工。需要傳遞的轉矩較大,片數(shù)較多。右離合器用來傳動主軸反轉,主要用于退回,片數(shù)較少。 這種離合器的工作原理是
22、,內(nèi)摩擦片的花鍵孔裝在軸Ⅰ的花鍵上,隨軸旋轉。外摩擦片的孔為圓孔,直徑略大于花鍵外徑。外圓上有4個凸起,嵌在空套齒輪的缺口之中。內(nèi)外摩擦片相間安裝。移動套筒4時,鋼球沿斜面向中心移動并使滑塊3、螺母1向左移動,將內(nèi)片與外片相互壓緊。軸Ⅰ的轉矩便通過摩擦片間的摩擦力矩傳遞給齒輪,使主軸正傳。同理,當滑塊7、螺母8向右時,使主軸反轉。處于中間位置時,左、右離合器都脫開,軸Ⅱ以后的各軸停轉。摩擦片的間隙可通過放松銷6和螺母8來進行調(diào)整。 摩擦片的軸向定位是由兩個帶花鍵孔的圓盤實現(xiàn)。其中一個圓盤裝在花鍵上,另一個裝在花鍵軸的一個環(huán)形溝槽里,并轉過一個花鍵齒,和軸上的花鍵對正,然后用螺釘把錯開的兩個圓
23、盤連接起來。 結構如下圖所示 3.3制動機構的設計 根據(jù)制動器的設計原理,將其安裝在靠近主軸的較高轉速的軸Ⅲ,在離合器脫開時制動主軸,以縮短輔助時間。此次設計采用帶式制動器。該制動器制動盤是一個鋼制圓盤,與軸用花鍵聯(lián)接,周邊圍著制動帶。制動帶是一條剛帶,內(nèi)側有一層酚醛石棉以增加摩擦。制動帶的一端與杠桿連接。另一端與箱體連接。為了操縱方便并保證離合器與制動器的聯(lián)鎖運動,采用一個操縱手柄控制。當離合器脫開時,齒條處于中間位置,將制動帶拉緊。齒條軸凸起的左、右邊都是凹槽。左、右離合器中任一個結合時,杠桿都按順時針方向擺動,使制動帶放松。 3.4齒輪塊的設計 機床的變速系統(tǒng)采用了
24、滑移齒輪變速機構。根據(jù)各傳動軸的工作特點,基本組(傳動組b)滑移齒輪采用平鍵聯(lián)接裝配式齒輪,固定齒輪用獨立式;第一擴大組(傳動組a)的滑移齒輪采用了整體式滑移齒輪;第二擴大組(傳動組c)傳動轉矩較大用平鍵聯(lián)接裝配式齒輪,此時平鍵傳遞轉矩,彈性擋圈軸向固定,簡單、工藝性好、結構方便。所有滑移齒輪與傳動軸間均采用花鍵聯(lián)接。 從工藝角度考慮,其他固定齒輪(主軸上的齒輪除外)也采用花鍵聯(lián)接。由于主軸直徑較大,為了降低加工成本而采用了單鍵聯(lián)接。 由各軸的圓周速度參考《設計指導》P53,Ⅰ~Ⅲ軸間傳動齒輪精度為8-7-7Dc,Ⅲ~Ⅳ軸間齒輪精度為7-6-6 Dc。 齒輪材料為45鋼,采用整體淬火處理
25、。 根據(jù)前面初估的模數(shù)計算齒輪直徑由于Ⅱ軸基本組的大齒輪會和離合器相干涉(相碰),因而對第一擴大組的齒輪模數(shù)進行調(diào)整,調(diào)為m=4mm,各齒輪參數(shù)如下表 齒輪 Z1 齒數(shù) 24 48 42 30 19 53 24 nj 950 475 950 1320 475 170 475 分度圓直徑 96 192 168 120 76 212 96 齒頂圓直徑 104 200 176 128 84 220 104 齒底圓直徑 86 182 158 110 66 202 86 齒輪寬 32 30
26、 30 32 32 30 32 齒輪 齒數(shù) 48 30 42 60 30 18 72 nj 236 475 335 170 335 475 118 分度圓直徑 192 120 168 240 120 72 288 齒頂圓直徑 200 128 176 248 128 80 296 齒底圓直徑 182 110 158 230 110 62 278 齒輪寬 30 32 30 30 32 33 30 3.5軸承的選擇 為了方便安裝,Ⅰ軸上傳動件的外徑均小于箱
27、體左側支承孔直徑,均采用深溝球軸承。為了便于裝配和軸承間隙調(diào)整,Ⅱ、Ⅲ軸均采用圓錐滾子軸承。滾動軸承均采用E級精度。 3.6主軸組件的設計 3.6.1各部分尺寸的選擇 3.6.1.1主軸通孔直徑 參考《設計指導》P5,取主軸通孔直徑d=37mm。 3.6.1.2軸頸直徑 據(jù)前面的估算主軸前軸頸直徑D1 = 80mm,后軸頸直徑D2 =60mm。 3.6.1.3前錐孔尺寸 據(jù)車床最大回轉直徑320mm,參考《設計指導》P61表莫氏錐度號選5;其標準莫氏錐度尺寸如下 簡圖 莫氏號 大端直徑D 錐度 長度 5 44.399 1:19.022
28、 130 3.6.1.4頭部尺寸的選擇 采用短圓錐式的頭部結構,懸伸短,剛度好。參考《設計指導》P63的圖及P64表的主軸頭部尺寸如下圖所示 3.6.1.5支承跨距及懸伸長度 為了提高剛度,應盡量縮短主軸的懸伸長度a,適當選擇支承跨距L。取L/a=3.24,由頭部尺寸取a=100mm則L=324mm。 3.6.2主軸軸承的選擇 為提高剛度,主軸采用三支承,前支承和中支承為主要支承,后支承為輔助支承。這是因為主軸上的傳動齒輪集中在前部;容易滿足主軸的最佳跨距要求;箱體上前、中支承的同軸度加工容易保證,尺寸公差也易控制。 前軸承選用一個型號為32316的圓錐滾子軸承,中軸
29、承選一個用型號為30214的圓錐滾子軸承,后軸承選用一個型號為6312深溝球軸承。前軸承D級精度,中軸承E級精度,后軸承E級精度。前軸承內(nèi)圈配合為k5,外圈配合為M6;中軸承內(nèi)圈配合為js5,外圈配合為K6;后軸承內(nèi)圈配合為js6,外圈配合為H7。 3.7潤滑系統(tǒng)的設計 主軸箱內(nèi)采用飛濺式潤滑,油面高度為65mm左右,甩油環(huán)浸油深度為10mm左右。潤滑油型號為:IIJ30。 卸荷皮帶輪軸承采用脂潤滑方式。潤滑脂型號為:鈣質(zhì)潤滑脂。 3.8密封裝置的設計 Ⅰ軸軸頸較小,線速度較低,為了保證密封效果,采用皮碗式接觸密封。而主軸直徑大、線速度較高,則采用了非接觸式密封。卸荷皮帶輪的潤滑采用
30、毛氈式密封,以防止外界雜物進入。詳見展開圖。 四、傳動件的驗算 4.1傳動軸的驗算 Ⅰ軸的剛度較低,故而在此處進行驗算。其受力簡化如下圖所示 ==9.55=9.55=80038 Nmm 齒輪受到的徑向力 =2tanα/=280038tan/96=606.9 N 對于傳動軸Ⅰ主要驗算軸上裝齒輪和軸承處的撓度y和傾角θ。Ⅰ軸上有一段為花鍵軸,但長度在軸上的比例不大,全軸按圓軸算。Ⅰ軸平均直徑求的d=31mm,則 截面慣性矩I===45333.2 按《設計指導》P34有關公式計算 對B點 y=/3EI = =1.28mm 查《設計指導》P33表 對一
31、般傳動軸許用撓度[Y]=(0.0003~0.0005)=(0.0003~0.0005)448=0.1464~0.244 mm; 對裝有齒輪的軸許用撓度[Y]=(0.01~0.03)m=(0.01~0.03)4=0.04~0.12 mm; 滿足要求。 = = =-3.56rad 查《設計指導》P33表許用[θ]=0.001rad 滿足要求。 對A點 = = =7.44rad 對C點 =- = =-9.46rad 查《設計指導》P33表許用[θ]=0.001rad 滿足要求。 綜上,Ⅰ軸的剛度滿足要求。 4.2鍵的驗算 4.2.1花鍵的
32、驗算 花鍵鍵側工作表面的擠壓應力為 ≤[] 式中:――計算擠壓應力;Mp ——花鍵傳遞的最大扭矩;Nm m =,N――該軸傳遞的最大功率,――該軸的計算轉速; D、d —— 花鍵的外徑和內(nèi)徑;mm z —— 花鍵的齒數(shù); ――工作長度;mm —— 載荷分布不均勻系數(shù),=0.7~0.8;?。?.75 []――許用擠壓應力,查《機械設計》表6-3,[]=100~140Mp,取[]=130 Mp; 對Ⅰ軸花鍵 ==80
33、038 Nm m 對Ⅰ軸裝離合器處花鍵 D=36mm d=32 mm z=8 =18 mm 則 =21.8 Mp≤[] 滿足要求。 對Ⅰ軸裝帶輪處花鍵 D=30mm d=26mm z=6 =40 mm 則 =12.7Mp≤[] 滿足要求。 所以Ⅰ軸花鍵滿足要求。 對Ⅱ軸花鍵 ==155274 Nm m D=46mm d=42mm z=8 =76 mm 則 =7.7Mp≤[] 滿足要求。 對Ⅲ軸花鍵 ==427974 Nm m D=50mm
34、d=46mm z=8 =126mm 則 =11.8Mp≤[] 滿足要求。 4.2.2平鍵的驗算 普通平鍵的強度條件 =≤[] 式中:――計算擠壓應力;Mp ——傳遞的轉矩;Nm —— 鍵與輪轂槽的接觸高度,=0.5h,此處h為鍵的高度;mm —— 鍵的工作長度;mm ――軸的直徑;mm []――鍵、軸、輪轂三者中最弱材料的許用擠壓應力,查《機械設計》表6-2,此處鍵、軸、輪轂三者材料都是鋼[]=100~120M Mp,取[]=110 Mp; 對Ⅱ軸三聯(lián)齒輪出A型平鍵 =155.274 Nm =0.5h=0
35、.54=2 mm =46 mm =53 mm 則 = =31.8 Mp≤[] 滿足要求。 對Ⅲ軸三聯(lián)齒輪出A型平鍵 =427.974 Nm =0.5h=0.57=3.5mm =62mm =63 mm 則 = =62.6 Mp≤[] 滿足要求。 對Ⅳ軸三聯(lián)齒輪出A型平鍵 ==1677Nm =0.5h=0.514=7mm =78mm =75 mm 則 = =81.9Mp≤[] 滿足要求。 4.3齒輪模數(shù)的驗算 按接觸疲勞強度計算齒輪模數(shù)mj mj = 16300mm
36、 式中:N —— 傳遞的額定功率KW; —— 計算轉速(小齒輪);r/min —— 齒寬系數(shù); z1 —— 計算齒輪齒數(shù); i —— 大齒輪與小齒輪齒數(shù)之比,“+”用于外嚙合,“—”用于內(nèi)嚙合,此處為外嚙合,故取“+”; —— 壽命系數(shù): = KTK nKNKq KT —— 工作期限系數(shù): KT = T——預定的齒輪工作期限,對中型機床 T = 15000~20
37、000h; n —— 齒輪的最低轉速;r/min c0 —— 基準循環(huán)次數(shù),查《設計指導》表3; m —— 疲勞曲線指數(shù),查《設計指導》表3; K n —— 轉速變化系數(shù),查《設計指導》表4; KN—— 功率利用系數(shù),查《設計指導》表5; Kq —— 材料強化系數(shù),查《設計指導》表6; Kc —— 工作狀況系數(shù),中等沖擊主運動,Kc = 1.2~1.6; Kd —— 動載荷
38、系數(shù),查《設計指導》表8; Kb —— 齒向載荷分布系數(shù),查《設計指導》表9; —— 許用接觸應力,查《設計指導》表11;Mp 齒輪按彎曲疲勞強度計算齒輪模數(shù)mw mw = 275 其中 Y —— 齒形系數(shù)由《設計指導》表10查得; —— 許用彎曲應力,查《設計指導》表11;Mp 驗算結果如下表 按接觸疲勞強度驗算算齒輪模數(shù) 參數(shù) 傳動組a 傳動組b 傳動組c N
39、 5.28 5.12 5.02 630 315 315 7.5 7.5 7.5 z1 24 19 18 i 2 2.8 4 m 3 3 3 n 630 315 112 T 15000 15000 15000 KT 3.84 3.05 2.16 1.44 0.88 0.81 c0 K n 0.85 0.68 0.89 KN 0.58 0.58 0.58 Kq 0.76 0.73 0.73 Kc 1.2 1.2 1.2 Kd 1.3
40、1.4 1.2 Kb 1.02 1.04 1.04 1100 1100 1100 mj 2.02 3.55 3.29 結論 估算值可用 估算值可用 估算值可用 齒輪按彎曲疲勞強度驗算齒輪模數(shù) 參數(shù) 傳動組a 傳動組b 傳動組c N 5.28 5.12 5.02 630 315 315 7.5 7.5 7.5 z1 24 19 18 m 6 6 6 n 630 315 112 T 15000 15000 15000 KT 2.56 2.28 1.92 0.9 0.
41、9 0.9 c0 K n 0.95 0.85 0.86 KN 0.78 0.78 0.78 Kq 0.77 0.75 0.75 Kc 1.2 1.2 1.2 Kd 1.3 1.4 1.2 Kb 1.02 1.04 1.04 320 320 320 Y 0.42 0.386 0.378 mw 1.83 3.09 3.01 結論 估算值可用 估算值可用 估算值可用 綜上,估算的模數(shù)值可用。 4.4軸承壽命的驗算 Lh=500≥[T
42、] 式中,Lh —— 額定壽命;h C —— 滾動軸承的額定動負荷;查《機械設計課程設計》第五章第三節(jié)常用滾動軸承部分;N —— 速度系數(shù), = ; —— 使用系數(shù);查《設計指南》表2.4-19; ε—— 壽命系數(shù),對于球軸承:ε= 3 ;對于滾子軸承:ε=10/3; ――功率利用系數(shù);查《設計指南》表2.4-20; ―― 轉速變化系數(shù);查《設計指
43、南》表2.4-21; —— 齒輪輪換工作系數(shù),查《設計指南》表2.4-27; P —— 當量動載荷N ; T ——滾動軸承許用使用壽命,一般取10000~15000h; 對Ⅰ軸的6406軸承受力如下圖 ===398N ===208.9N 附加軸向力 =0.2=79.6N =0.2=41.78N 軸向載荷 ==79.6N ==41.78N /=0.2 查《機械設計》表13-5 X=1 Y=0 查《機械設計》表13-6
44、 =1.5 得 =(X+Y) =1.5398 =597N 同理得 =312N 按計算 查表及計算有 C=47500N =0.375 =1.1 =0.80 ε=3 =0.97 =0.85 代入公式得 Lh=34769756h≥[T] 滿足要求 對Ⅱ軸的30208軸承受力如下圖 通過分析計算有 =588.7N =1487.2N 且兩者相互垂直 ==400N ==550.6N 則 ==680.6N 同理
45、 =955.4N 附加軸向力 =0.4=272.2N =0.4=382.2N 軸向載荷 ==272.2N ==382.2N /=0.4 查《機械設計》表13-5 X=1 Y=0 查《機械設計》表13-6 =1.5 得 =(X+Y) =1.5680.6 =1020.9N 同理得 =1433.1N 按計算 查表及計算有 C=63000N =0.5098 =1.1 =0.80 ε=10/3 =0.97 =0.85 代
46、入公式得 Lh=78259622h≥[T] 滿足要求 同理對Ⅲ軸的30208軸承滿足要求。 對主軸軸承當主(垂直)切削力與齒輪傳遞的力在同一平面內(nèi)且同向時主軸前軸承受力最大,如下圖所示,顯然驗算主軸的軸承壽命只驗算前軸承的32316型軸承。 由 108 +424 =324 得 =4632.9N 附加軸向力 =0.4=1853.16N= 對32316型軸承C=388000N =0.35 Y=1 查《機械設計》表13-5 X=0.4 Y=1 查《機械
47、設計》表13-6 =1.5 得 =(X+Y) =1.5(0.44632.9+1853.16) =5559.48N 查表及計算有 =0.769 =1.1 =0.80 ε=10/3 =0.97 =0.85 代入公式得 Lh=879306355h≥[T] 滿足要求 五、設計小結 這次機械加工設備課程設計是對車床主軸變速箱進行設計,是我們第一次較全面的金屬切削機床設計知識的綜合運用,通過這次練習,使得我們對金屬切削機床基礎知識有了一個
48、較為系統(tǒng)全面的認識,加深了對所學知識的理解和運用,將原來看來比較抽象的內(nèi)容實現(xiàn)了具體化,初步掊養(yǎng)了我們理論聯(lián)系實際的設計思想,訓練了綜合運用相關課程的理論,結合生產(chǎn)實際分析和解決工程實際問題的能力,鞏固、加深和擴展了有關方面的知識。 通過制訂設計方案,合理選擇各種參數(shù),以及針對課程設計中出現(xiàn)的問題查閱資料、相互討論、向老師請教等大大擴展了我們的知識面,培養(yǎng)了我們在本學科方面的興趣及實際動手能力,對將來我們在此方面的發(fā)展起了一個重要的作用。本次課程設計是我們對所學知識運用的一次嘗試,是我們在金屬切削機床知識學習方面的一次有意義的實踐。 在本次課程設計中,我獨立完成了自己的設計任務,通過這次設
49、計,弄懂了一些以前書本中難以理解的內(nèi)容,對以前所學知識的進行了鞏固。在設計中,通過老師的指導,使自己在設計思想、設計方法和設計技能等方面都得到了一次良好的訓練。 六、參考文獻 1.《機床主軸變速箱設計指導》 曹金榜 張玉峰等 編 2.《機械制造工藝金屬切削機床設計指南》 李洪 主編 東北工學院出版社 1989.3 3.《實用機床設計手冊》 4.《機床設計手冊》 機床設計手冊編寫組 編 機械工業(yè)出版社 1978.12 5.《金屬切削機床》 戴曙 主編 機械工業(yè)出版社 2008.4 6.《機械設計》 濮良貴 紀名剛 主編 高等教育出版社 2008.4 7.《機械制圖》 王蘭美 主編 高等教育出版社 2006.2 8.《材料力學》 劉鴻文 主編 高等教育出版社 2003.3 9.《機械設計課程設計》 周元康等 主編 重慶大學出版社 2007.2 10.《機械原理》 孫桓 陳作模 葛文杰 主編 高等教育出版社 2005.12 11.《機床設計圖冊》 上海紡織工學院編 1979.6 30
- 溫馨提示:
1: 本站所有資源如無特殊說明,都需要本地電腦安裝OFFICE2007和PDF閱讀器。圖紙軟件為CAD,CAXA,PROE,UG,SolidWorks等.壓縮文件請下載最新的WinRAR軟件解壓。
2: 本站的文檔不包含任何第三方提供的附件圖紙等,如果需要附件,請聯(lián)系上傳者。文件的所有權益歸上傳用戶所有。
3.本站RAR壓縮包中若帶圖紙,網(wǎng)頁內(nèi)容里面會有圖紙預覽,若沒有圖紙預覽就沒有圖紙。
4. 未經(jīng)權益所有人同意不得將文件中的內(nèi)容挪作商業(yè)或盈利用途。
5. 裝配圖網(wǎng)僅提供信息存儲空間,僅對用戶上傳內(nèi)容的表現(xiàn)方式做保護處理,對用戶上傳分享的文檔內(nèi)容本身不做任何修改或編輯,并不能對任何下載內(nèi)容負責。
6. 下載文件中如有侵權或不適當內(nèi)容,請與我們聯(lián)系,我們立即糾正。
7. 本站不保證下載資源的準確性、安全性和完整性, 同時也不承擔用戶因使用這些下載資源對自己和他人造成任何形式的傷害或損失。
最新文檔
- 2023年六年級數(shù)學下冊6整理和復習2圖形與幾何第7課時圖形的位置練習課件新人教版
- 2023年六年級數(shù)學下冊6整理和復習2圖形與幾何第1課時圖形的認識與測量1平面圖形的認識練習課件新人教版
- 2023年六年級數(shù)學下冊6整理和復習1數(shù)與代數(shù)第10課時比和比例2作業(yè)課件新人教版
- 2023年六年級數(shù)學下冊4比例1比例的意義和基本性質(zhì)第3課時解比例練習課件新人教版
- 2023年六年級數(shù)學下冊3圓柱與圓錐1圓柱第7課時圓柱的體積3作業(yè)課件新人教版
- 2023年六年級數(shù)學下冊3圓柱與圓錐1圓柱第1節(jié)圓柱的認識作業(yè)課件新人教版
- 2023年六年級數(shù)學下冊2百分數(shù)(二)第1節(jié)折扣和成數(shù)作業(yè)課件新人教版
- 2023年六年級數(shù)學下冊1負數(shù)第1課時負數(shù)的初步認識作業(yè)課件新人教版
- 2023年六年級數(shù)學上冊期末復習考前模擬期末模擬訓練二作業(yè)課件蘇教版
- 2023年六年級數(shù)學上冊期末豐收園作業(yè)課件蘇教版
- 2023年六年級數(shù)學上冊易錯清單十二課件新人教版
- 標準工時講義
- 2021年一年級語文上冊第六單元知識要點習題課件新人教版
- 2022春一年級語文下冊課文5識字測評習題課件新人教版
- 2023年六年級數(shù)學下冊6整理和復習4數(shù)學思考第1課時數(shù)學思考1練習課件新人教版