王圣波_汽車行李防護(hù)CAE仿真分析及優(yōu)化
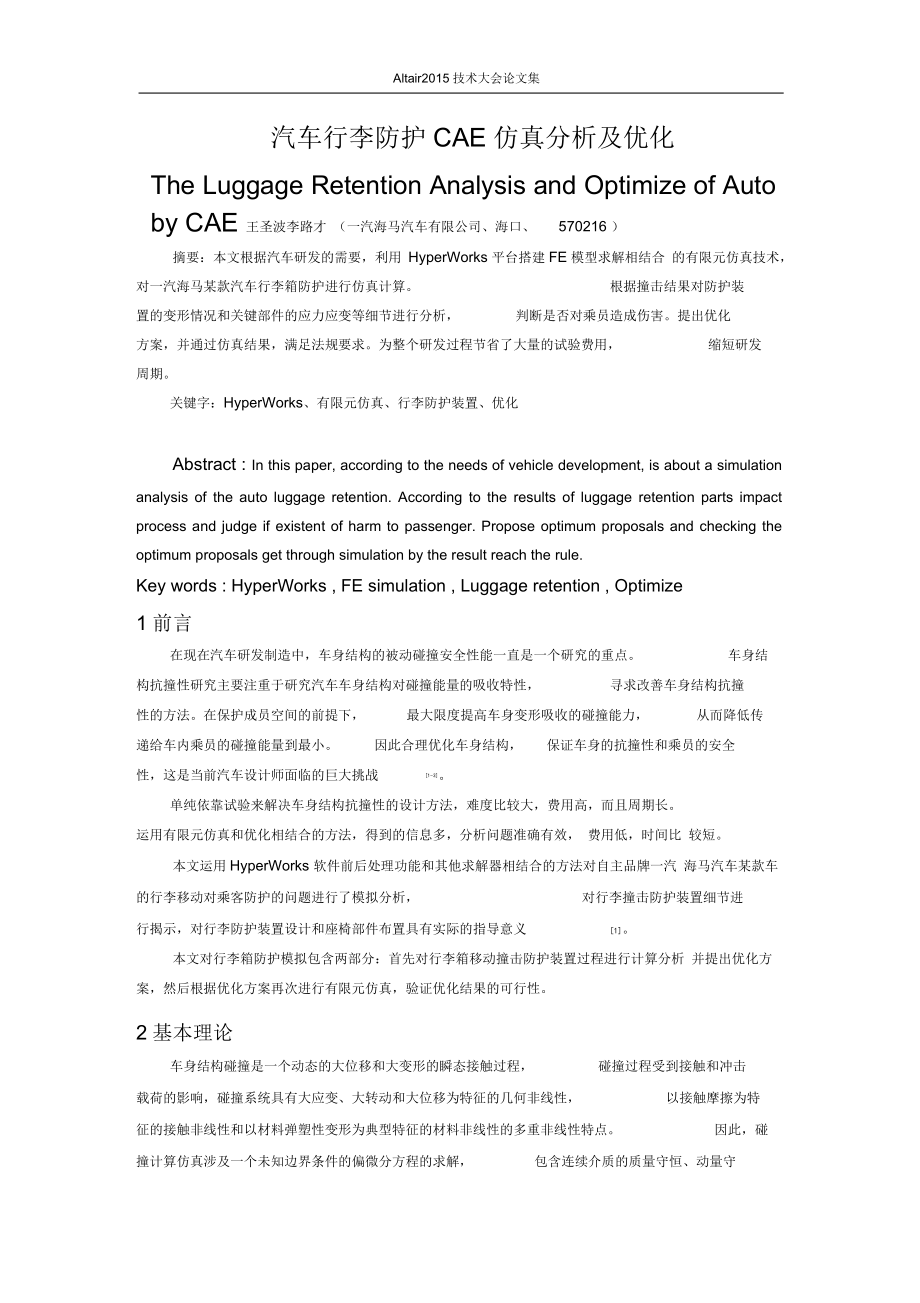


《王圣波_汽車行李防護(hù)CAE仿真分析及優(yōu)化》由會(huì)員分享,可在線閱讀,更多相關(guān)《王圣波_汽車行李防護(hù)CAE仿真分析及優(yōu)化(11頁珍藏版)》請(qǐng)?jiān)谘b配圖網(wǎng)上搜索。
1、Altair2015技術(shù)大會(huì)論文集 汽車行李防護(hù)CAE仿真分析及優(yōu)化 The Luggage Retention Analysis and Optimize of Auto by CAE 王圣波李路才 (一汽海馬汽車有限公司、???、 570216 ) 摘要:本文根據(jù)汽車研發(fā)的需要,利用 HyperWorks平臺(tái)搭建FE模型求解相結(jié)合 的有限元仿真技術(shù),對(duì)一汽海馬某款汽車行李箱防護(hù)進(jìn)行仿真計(jì)算。 根據(jù)撞擊結(jié)果對(duì)防護(hù)裝 置的變形情況和關(guān)鍵部件的應(yīng)力應(yīng)變等細(xì)節(jié)進(jìn)行分析, 判斷是否對(duì)乘員造成傷害。提出優(yōu)化 方案,并通過仿真結(jié)果,滿足法規(guī)要求。為整個(gè)研發(fā)過程節(jié)省了大量的試驗(yàn)費(fèi)用, 縮短研發(fā)
2、 周期。 關(guān)鍵字:HyperWorks、有限元仿真、行李防護(hù)裝置、優(yōu)化 Abstract : In this paper, according to the needs of vehicle development, is about a simulation analysis of the auto luggage retention. According to the results of luggage retention parts impact process and judge if existent of harm to passenger. Propose optimum
3、 proposals and checking the optimum proposals get through simulation by the result reach the rule. Key words : HyperWorks , FE simulation , Luggage retention , Optimize 1前言 在現(xiàn)在汽車研發(fā)制造中,車身結(jié)構(gòu)的被動(dòng)碰撞安全性能一直是一個(gè)研究的重點(diǎn)。 車身結(jié) 構(gòu)抗撞性研究主要注重于研究汽車車身結(jié)構(gòu)對(duì)碰撞能量的吸收特性, 尋求改善車身結(jié)構(gòu)抗撞 性的方法。在保護(hù)成員空間的前提下, 最大限度提高車身變形吸收的碰撞能力, 從而降
4、低傳 遞給車內(nèi)乘員的碰撞能量到最小。 因此合理優(yōu)化車身結(jié)構(gòu), 保證車身的抗撞性和乘員的安全 性,這是當(dāng)前汽車設(shè)計(jì)師面臨的巨大挑戰(zhàn) [1-3]。 單純依靠試驗(yàn)來解決車身結(jié)構(gòu)抗撞性的設(shè)計(jì)方法,難度比較大,費(fèi)用高,而且周期長(zhǎng)。 運(yùn)用有限元仿真和優(yōu)化相結(jié)合的方法,得到的信息多,分析問題準(zhǔn)確有效, 費(fèi)用低,時(shí)間比 較短。 本文運(yùn)用HyperWorks 軟件前后處理功能和其他求解器相結(jié)合的方法對(duì)自主品牌一汽 海馬汽車某款車的行李移動(dòng)對(duì)乘客防護(hù)的問題進(jìn)行了模擬分析, 對(duì)行李撞擊防護(hù)裝置細(xì)節(jié)進(jìn) 行揭示,對(duì)行李防護(hù)裝置設(shè)計(jì)和座椅部件布置具有實(shí)際的指導(dǎo)意義 [1]。 本文對(duì)行李箱防護(hù)模擬包含兩部分:
5、首先對(duì)行李箱移動(dòng)撞擊防護(hù)裝置過程進(jìn)行計(jì)算分析 并提出優(yōu)化方案,然后根據(jù)優(yōu)化方案再次進(jìn)行有限元仿真,驗(yàn)證優(yōu)化結(jié)果的可行性。 2基本理論 車身結(jié)構(gòu)碰撞是一個(gè)動(dòng)態(tài)的大位移和大變形的瞬態(tài)接觸過程, 碰撞過程受到接觸和沖擊 載荷的影響,碰撞系統(tǒng)具有大應(yīng)變、大轉(zhuǎn)動(dòng)和大位移為特征的幾何非線性, 以接觸摩擦為特 征的接觸非線性和以材料彈塑性變形為典型特征的材料非線性的多重非線性特點(diǎn)。 因此,碰 撞計(jì)算仿真涉及一個(gè)未知邊界條件的偏微分方程的求解, 包含連續(xù)介質(zhì)的質(zhì)量守恒、動(dòng)量守 恒和能量守恒,整個(gè)運(yùn)動(dòng)系統(tǒng)滿足以下各項(xiàng)條件: 運(yùn)動(dòng)方程 在有限元模型中每一個(gè)節(jié)點(diǎn)位置和時(shí)間的關(guān)系表達(dá)式為 X = X
6、(X,t) 在t = 0時(shí),初始位置為 X( M ,0)=立 ? Xi ( Xa ,0) = Vi Xa 其中,X為初始時(shí)刻的質(zhì)點(diǎn)坐標(biāo), t為質(zhì)點(diǎn)運(yùn)動(dòng)的時(shí)間,vi(i = 1,2,3 )為質(zhì)點(diǎn)的初始 速度。 動(dòng)量守恒方程 ? (Tij - + P ?fi = P ? X ?才 ■ ■ 式中o-ij為Cauchy應(yīng)力;f i (i = 1,2,3 )為單位質(zhì)量體積力; x為質(zhì)點(diǎn)加速度。 質(zhì)量守恒方程 p = J po 式中,p為當(dāng)前質(zhì)量密度, po為初始質(zhì)量密度,J為密度變化系數(shù)。 面力邊界條件: ?"師 ni = T(t) 式中n(i = 1,2,3 )為?b邊
7、界單元的單位法向量, T(i = 1,2,3)為面力載荷。 位移邊界條件: ?b2 才(X,t) = ki(t) 式中,ki(t), i = 1,2,3是給定位移函數(shù) 接觸內(nèi)邊界條件: ?b3( of -叼-)?n = 0 當(dāng)(為+ =才)接觸時(shí)沿接觸邊界 由上述各方程及邊界條件得到虛功原理的變分列式: 8 =/x 8加+ ”必-JP?fi 8心-?小,靜=0其物理意義:作用在物體上的外力和內(nèi)力的虛 功之和為零。 3法規(guī)要求 GB15083-2006《汽車座椅、座椅固定裝置及頭枕強(qiáng)度》是汽車被動(dòng)安全的一個(gè)重要標(biāo) 準(zhǔn),是車輛公告試驗(yàn)的強(qiáng)制檢查項(xiàng)目。 標(biāo)準(zhǔn)中關(guān)于防止移動(dòng)行李
8、對(duì)乘員傷害有特殊要求, 構(gòu) 成行李艙的座椅靠背和頭枕應(yīng)具有足夠的強(qiáng)度以保護(hù)乘員不因行李的前移而受到傷害。 試驗(yàn) 過程中座椅及其鎖止裝置需保持在原位置, 試驗(yàn)期間允許座椅靠背及其緊固件變形, 條件是 隔離裝置部分(包括試驗(yàn)的座椅靠背和頭枕) [邵爾(A)硬度大于50]部分的前輪廓不能 向前方移出一橫向垂面,此平面經(jīng)過 [2]: a)座椅的R直前方150mm處的點(diǎn)(對(duì)頭枕部分),如圖 1所示B面線; b)座椅的R點(diǎn)前方100mm處得點(diǎn)(座椅靠背部分),如圖 1所示A面線。 圖1試驗(yàn)邊界條件 圖2試驗(yàn)樣塊布置 3.1 試驗(yàn)條件 3.1.1 試驗(yàn)樣塊 試驗(yàn)樣塊,使用2塊剛性試驗(yàn)
9、樣塊代替行李箱,要求其慣性中心與幾何中心重合。尺寸 均為:300mme 300mme 300mm ; 一切邊棱倒圓角均為 20mm ;質(zhì)量為:18kg。 3.1.2 試驗(yàn)樣塊布置 將試驗(yàn)樣塊放置在行李艙底部, 其前部與構(gòu)成行李艙邊界的車輛部件接觸, 然后沿平行 于車輛的縱向中心方向?qū)⑵湎蚝笠苿?dòng), 直至其質(zhì)心移動(dòng)200mm的水平距離(如圖1所示)。 車輛縱向中心面與各試驗(yàn)樣塊內(nèi)側(cè)邊緣的距離應(yīng)該為 25mm,以使兩樣塊之間有 50mm的距 離(如圖2所示)。 3.1.3 試驗(yàn)方法 將車體固定在試驗(yàn)臺(tái)車上。車體裝在臺(tái)車上的連接方式不應(yīng)對(duì)座椅靠背和 隔離系統(tǒng)有所加強(qiáng)。按照2.2.
10、2的方式放置試驗(yàn)樣塊,對(duì)乘員車體進(jìn)行減速,法 規(guī)對(duì)減速度波形上下限有嚴(yán)格要求,本文為了模擬最苛刻的減速度工況,采用 減速度斜率最大的減速方式(如圖 3所示)。減速前,乘員車體的自由速度為 50+2km/ h。 曲 仲 曲 0 m Tivm 困 D S 5 一aJLjcHlHJIla9U04 圖3減速度曲線 4有限元模型的建立 4.1網(wǎng)格劃分 為了節(jié)省建模時(shí)間和提高建模效率,去除轉(zhuǎn)向系 統(tǒng)、動(dòng)力系統(tǒng)、前排座椅和底盤等對(duì)行李位移防護(hù)影 響微弱的總成,并根據(jù)法規(guī)將邵爾( A)硬度小于 50 的坐墊、頭枕等泡棉撤除 [3],僅保留后排座椅和后白 車身兩大系統(tǒng)總成。為了能夠精準(zhǔn)模擬行
11、李位移沖擊 乘客防護(hù)裝置的細(xì)節(jié),建模過程中,盡量保留幾何特 征(如圖4)。 白車身內(nèi)部結(jié)構(gòu)復(fù)雜,零部件繁多,全部采用 抽取中面畫殼單元面網(wǎng)格的方法處理,面網(wǎng)格尺寸 按10mm的標(biāo)準(zhǔn)劃分,以保證零部件幾何特征得到 精確再現(xiàn),對(duì)座椅安裝支架、座椅骨架和頭枕骨架 等局部強(qiáng)度計(jì)算,采用5mm的尺寸標(biāo)準(zhǔn)(如圖5)。 網(wǎng)格劃分完以后對(duì)零部件進(jìn)行材料和厚度屬性的賦 予,檢查網(wǎng)格干涉、穿透,然后根據(jù)焊點(diǎn)位置打焊 點(diǎn),做連接。整個(gè) FE模型總共由294060個(gè)節(jié)點(diǎn), 266177 個(gè)殼單元,2149個(gè)焊點(diǎn)單元和 2576個(gè)膠 粘等體單元組成。 4.2材料條件 圖5后白車身內(nèi)
12、 行李位移重點(diǎn)關(guān)注對(duì)后排座椅的沖擊過程, 后排座椅是關(guān)鍵考察對(duì)象,具體材料和厚度 本構(gòu)關(guān)系,屈服條件考慮材料的應(yīng)變率。 如圖6所示,材料模型使用 Cowper-Symonds 圖6后白車身內(nèi)部面網(wǎng) 圖7減速度方向 4.3邊界條件 根據(jù)GB15083-2006 的試驗(yàn)要求,約束車身 Y和Z方向
13、的平動(dòng)和 X、Y和Z方向的轉(zhuǎn) 動(dòng)放開X方向(即整車的前進(jìn)方向)的平動(dòng)自由度。對(duì)車身進(jìn)行減速度加載,按圖 3的減 速度和時(shí)間曲線加載,加載方向如圖 7所示。 完成以上相關(guān)參數(shù)設(shè)定后,從 HyperMesh軟件中導(dǎo)出包含所有參數(shù)信息的 FE模型的 k文件,提交到服務(wù)器上,應(yīng)用求解器進(jìn)行計(jì)算。 5計(jì)算結(jié)果及優(yōu)化 圖8初次仿真變形結(jié)果圖 5.1仿真結(jié)果分析 根據(jù)計(jì)算結(jié)果顯示(如圖 8),車輛減速過程中, 行李向前移動(dòng)撞擊后排座椅,后排座椅變形較為嚴(yán) 重,所以重點(diǎn)考察座椅的變形情況。從圖 9和圖10 中可知,座椅頭枕侵入量超過 R點(diǎn)前方150mm的參 考平面,最大值為:-63mm@102.
14、5ms ;座椅骨架侵 入量超過R點(diǎn)前方100mm參考平面,最大值為: -12.2mm@107.5ms ,未能達(dá)到法規(guī)要求。 座椅的安裝支架強(qiáng)度不足,變形扭 通過分析行李撞擊防護(hù)裝置過程, 從圖8可以看1 曲嚴(yán)重,導(dǎo)致座椅底部前傾, 帶動(dòng)座椅骨架和頭枕骨架向前方移動(dòng), 移動(dòng)數(shù)值均超過法規(guī)要 求的界限。說明該行李移動(dòng)防護(hù)裝置方案對(duì)乘員保護(hù)性能不足。 表1初次仿真座椅及固定點(diǎn)塑性變形 零部件 座椅骨架 座椅連接支架 座椅安裝地板 塑性變形目標(biāo) 30% 30% 15% 最大塑性應(yīng)變 32% 9.5% 3.1% 150m (EE) KUBISaXQs 頭枕骨
15、架最大位移 座椅It消最大付移 Min. -62.9000.1025 5000000O1TO 4540S5州252015105 OB 12 圖9初次仿真座椅靠背骨架和頭枕骨架向前位移圖 圖10測(cè)量目標(biāo)到基準(zhǔn)平面的位移量 i.Q63E-02 L307E-Q2 C-nnLour Plpt LiractiR/fi plaslic: stram(bcalar unlu% Sirrifjle Avtiyge ■i No rccutl Mak - X nmE: Mode 1D1-2&2G Min = n nnnF i-m Mode 101S1911 |_5 1-1 nlUB-
16、r
崎
h il M
LLLMLUI
"k!L
IJ 17、塑性變形目標(biāo);座椅連
9.5%,在變性目標(biāo)范圍內(nèi);車身安裝點(diǎn)的最大塑性變形目標(biāo)為
3.1%,符合工程設(shè)計(jì)目標(biāo)要求。
5.2 優(yōu)化方案
由5.1的分析結(jié)果座椅頭枕骨架和座椅靠背骨架移動(dòng)量均超過了 GB15083-2006法規(guī)
的要求。通過對(duì)比圖 4和圖8行李移動(dòng)前后防護(hù)裝置的變化圖,從座椅骨架及其安裝支架
變形模式可以看出,座椅骨架前傾量較大主要原因?yàn)樽伟惭b支架強(qiáng)度不足變形較大如圖 8
紅圈標(biāo)示。因此,需要對(duì)座椅安裝支架進(jìn)行優(yōu)化,具體優(yōu)化方案如表 2所示。其中,前排
左右支架均與地板支架用兩個(gè)螺栓連接,后排左右支架分別通過兩個(gè)螺栓與座椅固定。
5.3 優(yōu)化結(jié)果分析
18、
如圖12所示,優(yōu)化后座椅頭枕骨架向前移動(dòng)未超過 R點(diǎn)前方150mm的參考平面,座
椅靠背骨架向前移動(dòng)未超過 R點(diǎn)前方90mm參考平面,達(dá)到法規(guī)要求。頭枕骨架距離基準(zhǔn)
平面的距離為183mm@95ms ,座椅靠背骨架距離其基準(zhǔn)平面的最小距離為 108.4mm@80ms ,安全裕度值較大(如圖 13)。從圖12和表3中得到,優(yōu)化后座椅骨架
最大塑性變形為 26% ,座椅連接支架最大塑性變形為 12.7% ,座椅支架地板安裝點(diǎn)最大塑
性變形為3.1%,以上最大塑性應(yīng)變均在工程設(shè)計(jì)目標(biāo)范圍內(nèi),優(yōu)化方案符合設(shè)計(jì)要求。
圖12優(yōu)化后座椅靠背骨架
圖13優(yōu)化后測(cè)量目標(biāo)和頭
枕骨架 19、向前位移圖
到基準(zhǔn)平面的位移量
表3優(yōu)化后座椅及固定點(diǎn)塑性變形
零部件
座椅骨架
座椅連接支架
座椅安裝地板
塑性應(yīng)變目標(biāo)
30%
30%
15%
最大塑性應(yīng)變
26%
12.7%
3.1%
Urfq. Fl.
EITaci/Ft Bi lafXSuLar q aIua
t泗
2 用CEOS
11血血
|r-6A25EC0 IL? ai13E
20、 msiil: M笊=d.拄|=4J1 ELEHEHT
Carinur Plirl
E觸疝帕城喇h陽二:白固網(wǎng)U* Ma力 2.624 E-01
Q ZPIZ.m
2.D4IEETI
174.9BEJ1
l.ltJJE-Ln
1 if^RDi
6745E 02
5.E3OED2
上心KLQ
炳口 = o nfi三心I
CviMinii: Msj. Vwlue - E.2S2
CnrtoL- PH F/由rt力r pl^Afln用門加尸由wlwr tl 257E-D1
11JEL=>U1
9.LKGED2
—a.4xSE-D2
,工MED2 EHlE-n?
I 21、 -4.224匚 D2
I-2.616E-D2
I UXHE-rQ
Ln rmF-rri ■ hn r^Riill 工
Max - 1 JG?L 01
ELE^ENT_SHELL d104Mi Mm = U LUjI="HJJ
EUEr/ENT SHELL 41Q4劃二
■I indriflAK
Oynamc Man. VoIjc - D. 127
EU&MEnn SHELL 4103ZEB3
圖14優(yōu)化、后座椅及固定點(diǎn)塑性變形
6總結(jié)
本文通過HyperWorks 和仿真平臺(tái)對(duì)研發(fā)過程中海馬某款車的行李移動(dòng)撞擊防護(hù)裝置 過程進(jìn)行模擬分析,并針對(duì)分析過程中存在影響乘 22、員生存空間的問題提出優(yōu)化措施。 優(yōu)化結(jié)
果符合GB15083-2006 法規(guī)要求,能夠?qū)⑵嚰蓖r(shí)行李移動(dòng)沖擊乘員安全問題隱患扼制 在研發(fā)初期階段。大大降低了研發(fā)周期,減少重復(fù)性的試驗(yàn)費(fèi)用,具有指導(dǎo)意義。
7參考文獻(xiàn)
[1 ]胡玉梅.汽車正面碰撞設(shè)計(jì)分析技術(shù)及應(yīng)用研究 .重慶大學(xué)博士學(xué)位論文,2002.9.
[2]胡遠(yuǎn)志,曾必強(qiáng),謝書港.給予HyperWorks的汽車安全仿真分析.北京:清華大學(xué)出版社, 2011.
[3]彭昌坤.汽車車身結(jié)構(gòu)正面碰撞仿真分析 .中國農(nóng)業(yè)大學(xué)碩士學(xué)位論文, 2007.
[4]GB15083-2006 汽車座椅、座椅固定裝置及頭枕強(qiáng)度要求和試驗(yàn)方法, 2006.
- 溫馨提示:
1: 本站所有資源如無特殊說明,都需要本地電腦安裝OFFICE2007和PDF閱讀器。圖紙軟件為CAD,CAXA,PROE,UG,SolidWorks等.壓縮文件請(qǐng)下載最新的WinRAR軟件解壓。
2: 本站的文檔不包含任何第三方提供的附件圖紙等,如果需要附件,請(qǐng)聯(lián)系上傳者。文件的所有權(quán)益歸上傳用戶所有。
3.本站RAR壓縮包中若帶圖紙,網(wǎng)頁內(nèi)容里面會(huì)有圖紙預(yù)覽,若沒有圖紙預(yù)覽就沒有圖紙。
4. 未經(jīng)權(quán)益所有人同意不得將文件中的內(nèi)容挪作商業(yè)或盈利用途。
5. 裝配圖網(wǎng)僅提供信息存儲(chǔ)空間,僅對(duì)用戶上傳內(nèi)容的表現(xiàn)方式做保護(hù)處理,對(duì)用戶上傳分享的文檔內(nèi)容本身不做任何修改或編輯,并不能對(duì)任何下載內(nèi)容負(fù)責(zé)。
6. 下載文件中如有侵權(quán)或不適當(dāng)內(nèi)容,請(qǐng)與我們聯(lián)系,我們立即糾正。
7. 本站不保證下載資源的準(zhǔn)確性、安全性和完整性, 同時(shí)也不承擔(dān)用戶因使用這些下載資源對(duì)自己和他人造成任何形式的傷害或損失。
最新文檔
- 建筑施工重大危險(xiǎn)源安全管理制度
- 安全培訓(xùn)資料:典型建筑火災(zāi)的防治基本原則與救援技術(shù)
- 企業(yè)雙重預(yù)防體系應(yīng)知應(yīng)會(huì)知識(shí)問答
- 8 各種煤礦安全考試試題
- 9 危險(xiǎn)化學(xué)品經(jīng)營(yíng)單位安全生產(chǎn)管理人員模擬考試題庫試卷附答案
- 加壓過濾機(jī)司機(jī)技術(shù)操作規(guī)程
- 樹脂砂混砂工藝知識(shí)總結(jié)
- XXXXX現(xiàn)場(chǎng)安全應(yīng)急處置預(yù)案
- 某公司消防安全檢查制度總結(jié)
- 1 煤礦安全檢查工(中級(jí))職業(yè)技能理論知識(shí)考核試題含答案
- 4.燃?xì)獍踩a(chǎn)企業(yè)主要負(fù)責(zé)人模擬考試題庫試卷含答案
- 工段(班組)級(jí)安全檢查表
- D 氯化工藝作業(yè)模擬考試題庫試卷含答案-4
- 建筑起重司索信號(hào)工安全操作要點(diǎn)
- 實(shí)驗(yàn)室計(jì)量常見的30個(gè)問問答題含解析