畢業(yè)設計(論文)甲烷電控單元支架沖壓模
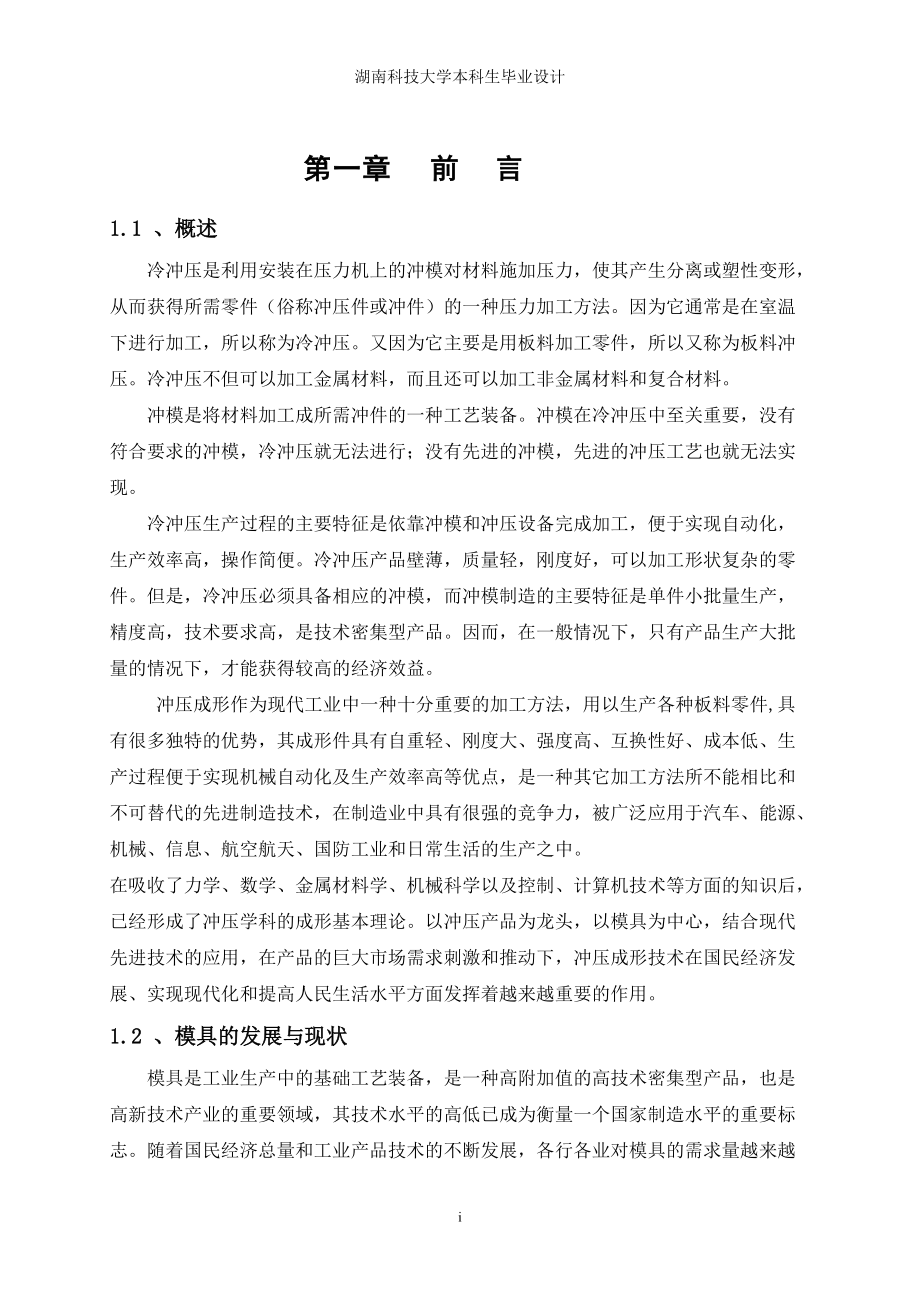


《畢業(yè)設計(論文)甲烷電控單元支架沖壓?!酚蓵T分享,可在線閱讀,更多相關《畢業(yè)設計(論文)甲烷電控單元支架沖壓模(43頁珍藏版)》請在裝配圖網(wǎng)上搜索。
1、湖南科技大學本科生畢業(yè)設計 第一章 前 言 1.1 、概述 冷沖壓是利用安裝在壓力機上的沖模對材料施加壓力,使其產(chǎn)生分離或塑性變形,從而獲得所需零件(俗稱沖壓件或沖件)的一種壓力加工方法。因為它通常是在室溫下進行加工,所以稱為冷沖壓。又因為它主要是用板料加工零件,所以又稱為板料沖壓。冷沖壓不但可以加工金屬材料,而且還可以加工非金屬材料和復合材料。 沖模是將材料加工成所需沖件的一種工藝裝備。沖模在冷沖壓中至關重要,沒有符合要求的沖模,冷沖壓就無法進行;沒有先進的沖模,先進的沖壓工藝也就無法實現(xiàn)。 冷沖壓生產(chǎn)過程的主要特征是依靠沖模和沖壓設備完成加工,便于實現(xiàn)自動化,生產(chǎn)效率高,操作
2、簡便。冷沖壓產(chǎn)品壁薄,質量輕,剛度好,可以加工形狀復雜的零件。但是,冷沖壓必須具備相應的沖模,而沖模制造的主要特征是單件小批量生產(chǎn),精度高,技術要求高,是技術密集型產(chǎn)品。因而,在一般情況下,只有產(chǎn)品生產(chǎn)大批量的情況下,才能獲得較高的經(jīng)濟效益。 沖壓成形作為現(xiàn)代工業(yè)中一種十分重要的加工方法,用以生產(chǎn)各種板料零件,具有很多獨特的優(yōu)勢,其成形件具有自重輕、剛度大、強度高、互換性好、成本低、生產(chǎn)過程便于實現(xiàn)機械自動化及生產(chǎn)效率高等優(yōu)點,是一種其它加工方法所不能相比和不可替代的先進制造技術,在制造業(yè)中具有很強的競爭力,被廣泛應用于汽車、能源、機械、信息、航空航天、國防工業(yè)和日常生活的生產(chǎn)之中。 在吸
3、收了力學、數(shù)學、金屬材料學、機械科學以及控制、計算機技術等方面的知識后,已經(jīng)形成了沖壓學科的成形基本理論。以沖壓產(chǎn)品為龍頭,以模具為中心,結合現(xiàn)代先進技術的應用,在產(chǎn)品的巨大市場需求刺激和推動下,沖壓成形技術在國民經(jīng)濟發(fā)展、實現(xiàn)現(xiàn)代化和提高人民生活水平方面發(fā)揮著越來越重要的作用。 1.2 、模具的發(fā)展與現(xiàn)狀 模具是工業(yè)生產(chǎn)中的基礎工藝裝備,是一種高附加值的高技術密集型產(chǎn)品,也是高新技術產(chǎn)業(yè)的重要領域,其技術水平的高低已成為衡量一個國家制造水平的重要標志。隨著國民經(jīng)濟總量和工業(yè)產(chǎn)品技術的不斷發(fā)展,各行各業(yè)對模具的需求量越來越大,技術要求也越來越高。目前我國模具工業(yè)的發(fā)展步伐日益加快,產(chǎn)品發(fā)展
4、重點主要應表現(xiàn)在: (1)汽車覆蓋件模; (2)精密沖模; (3)大型及精密塑料模; (4)主要模具標準件; (5)其它高技術含量的模具。 目前我國模具年生產(chǎn)總量雖然已位居世界第三,其中,沖壓模占模具總量的40%以上[2],但在整個模具設計制造水平和標準化程度上,與德國、美國、日本等發(fā)達國家相比還存在相當大的差距。以大型覆蓋件沖模為代表,我國已能生產(chǎn)部分轎車覆蓋件模具。轎車覆蓋件模具設計和制造難度大,質量和精度要求高,代表覆蓋件模具的水平。在設計制造方法、手段上已基本達到了國際水平,模具結構功能方面也接近國際水平,在轎車模具國產(chǎn)化進程中前進了一大步。但在制造質量、精度、制造周期和成
5、本方面,以國外相比還存在一定的差距。標志沖模技術先進水平的多工位級進模和多功能模具,是我國重點發(fā)展的精密模具品種,在制造精度、使用壽命、模具結構和功能上,與國外多工位級進模和多功能模具相比,存在一定差距。 1.3 、課題的主要特點及意義 該課題主要針對甲烷電控單元支架零件(如圖1-1),在對單元支架進行沖孔、落料和壓彎等成形工藝分析的基礎上,提出了該零件采用多工位級進模的沖壓方案;根據(jù)零件的形狀、尺寸精度要求,保證工件的尺寸和形狀位置精度要求的同時,提高了材料的利用率和勞動生產(chǎn)率。 圖1-1 甲烷電控單元支架立體圖 本課題涉及的知識面廣,綜合性較強,在鞏固大學所學知識的同時,對于提
6、高設計者的創(chuàng)新能力、協(xié)調能力,開闊設計思路等方面為作者提供了一個良好的平臺。 1.4、 沖壓工藝與模具設計的內容及步驟 沖壓工藝與模具設計是進行沖壓生產(chǎn)的重要技術準備工作。沖壓工藝與模具設計應結合工廠的設備、人員等實際情況,從零件的質量、生產(chǎn)效率、生產(chǎn)成本、勞動強度、環(huán)境的保護以及生產(chǎn)的安全性各個方面綜合考慮,選擇和設計出技術先進、經(jīng)濟上合理、使用安全可靠的工藝方案和模具結構,以使沖壓件的生產(chǎn)在保證達到設計圖樣上所提出的各項技術要求的基礎上,盡可能降低沖壓的工藝成本和保證安全生產(chǎn)。一般來講,設計的主要內容及步驟包括: 1.4.1、工藝設計 (1) 零件及其沖壓工藝性分析 根據(jù)沖壓件
7、產(chǎn)品圖,分析沖壓件的形狀特點、尺寸大小、精度要求、原材料尺寸規(guī)格和力學性能,并結合可供選用的沖壓設備規(guī)格以及模具制造條件、生產(chǎn)批量等因素,分析零件的沖壓工藝性。良好的沖壓工藝性應保證材料消耗少、工序數(shù)目少、占用設備數(shù)量少、模具結構簡單而壽命高、產(chǎn)品質量穩(wěn)定、操作簡單。 (2) 確定工藝方案,主要工藝參數(shù)計算 在沖壓工藝性分析的基礎上,找出工藝與模具設計的特點與難點,根據(jù)實際情況提出各種可能的沖壓工藝方案,內容包括工序性質、工序數(shù)目、工序順序及組合方式等。有時同一種沖壓零件也可能存在多個可行的沖壓工藝方案,通常每種方案各有優(yōu)缺點,應從產(chǎn)品質量、生產(chǎn)效率、設備占用情況、模具制造的難易程度和壽
8、命高低、生產(chǎn)成本、操作方便與安全程度等方面進行綜合分析、比較,確定出適合于現(xiàn)有生產(chǎn)條件的最佳方案。 此外,了解零件的作用及使用要求對零件沖壓工藝與模具設計是有幫助的。 工藝參數(shù)指制定工藝方案所依據(jù)的數(shù)據(jù),如各種成形系數(shù)(拉深系數(shù)、脹形系數(shù)等)、零件展開尺寸以及沖裁力、成形力等。計算有兩種情況,第一種是工藝參數(shù)可以計算得比較準確,如零件排樣的材料利用率、沖裁壓力中心、工件面積等;第二種是工藝參數(shù)只能作近似計算,如一般彎曲或拉深成形力、復雜零件坯料展開尺寸等,確定這類工藝參數(shù)一般是根據(jù)經(jīng)驗公式或圖表進行粗略計算,有些需通過試驗調整;有時甚至沒有經(jīng)驗公式可以應用,或者因計算太繁雜以致于無法進行,
9、如復雜模具零件的剛性或強度校核、復雜沖壓零件成形力計算等,這種情況下一般只能憑經(jīng)驗進行估計。 (3) 選擇沖壓設備 根據(jù)要完成的沖壓工序性質和各種沖壓設備的力能特點,考慮沖壓加工所需的變形力、變形功及模具閉合高度和輪廓尺寸的大小等主要因素,結合工廠現(xiàn)有設備情況來合理選定設備類型和噸位。 常用沖壓設備有曲柄壓力機、液壓機等,其中曲柄壓力機應用最廣。沖裁類沖壓工序多在曲柄壓力機上進行,一般不用液壓機;而成形類沖壓工序可在曲柄壓力機或液壓機上進行。 1.4.2 、模具設計 模具設計包括模具結構形式的選擇與設計、模具結構參數(shù)計算、模具圖繪制等內容。 (1) 模具結構形式的選擇與設計
10、根據(jù)擬定的工藝方案,考慮沖壓件的形狀特點、零件尺寸大小、精度要求、生產(chǎn)批量、模具加工條件、操作方便與安全的要求等選定與設計沖模結構形式。 (2) 模具結構參數(shù)計算 確定模具結構形式后,需計算或校核模具結構上的有關參數(shù),如模具工作部分(凸、凹模等)的幾何尺寸、模具零件的強度與剛度、模具運動部件的運動參數(shù)、模具與設備之間的安裝尺寸,選用和核算彈性元件等。 (3) 繪制模具圖 模具圖是沖壓工藝與模具設計結果的最終體現(xiàn),一套完整的模具圖應該包括模具和使用模具的完備信息。模具圖的繪制應該符合國家制定的制圖標準,同時考慮模具行業(yè)的特殊要求與習慣。 模具圖由總裝圖和非標準件的零件圖組成??傃b配
11、圖主要反映整個模具各個零件之間的裝配關系,應該對應繪制說明模具構造的投影圖,主要是主視圖和俯視圖及必要的剖面、剖視圖,并注明主要結構尺寸,如閉合高度、輪廓尺寸等。習慣上俯視圖由下模部分投影而得,同時在圖紙的右上角繪出工件圖、排樣圖,右下方列出模具零件的明細表,寫明技術要求等。零件圖一般根據(jù)模具總裝配圖測繪,也應該有足夠的投影各必要的剖面、剖視圖以將零件結構表達清楚。此外,要標注零件加工所需的所有結構尺寸、公差、表面粗糙度、熱處理及其他技術要求。 對于一個完整的生產(chǎn)過程,沖壓工藝與模具設計是密不可分的,二者相互聯(lián)系,相互影響,因此前述督可能需要交叉、反復進行。若方案有變化,則需重新進行設計計算
12、。 1.4.3 、編寫工藝文件及設計計算說明書 為了規(guī)范生產(chǎn),加強管理,每一種沖壓產(chǎn)品的生產(chǎn)需寫相應的工藝文件(如工序卡片)。對零件沖壓工藝和模具設計應編寫設計計算說明書,以供日后查閱。設計計算說明書應該包括沖壓件的工藝分析以及模具設計的主要內容。進行必要的工藝計算,主要包括: a.排樣設計與計算。選擇排樣方法、確定搭邊值、計算送料步距與條料寬度、計算材料利用率、畫出排樣圖等。 b.計算沖壓力。包括沖裁力、缷料力、推件力或頂件力等。根據(jù)沖壓力選擇壓力機的噸位。 c.計算模具壓力中心。 d.計算凸、凹模工作部分尺寸并確定其制造公差。 e.彈性元件的選用與計算。 f.必要時,對模具
13、的主要零部件進行強度驗算。 第二章 級進模簡介 級進模又稱跳步模,它是在一副模具內,分為若干個等距離沖壓工位,對被加工材料(一般稱為帶料或條料)在控制送進距離機構的控制下,逐個進行沖壓,便得到一個完整的沖壓零件。這樣,一個比較復雜的沖壓零件,用一副多工位(沖裁是由凸模和凹模完成,凸模和凹模組成一組刀口,把材料壓在中間,凸模逐步靠近凹模,使材料分離;彎曲是利用壓力使材料產(chǎn)生塑性變形,從而被彎成有一定曲率、一定角度的形狀的一種沖壓工序;整形是依靠材料流動,少量改變工序件形狀和尺寸,以保證工件精度的一種沖壓工序) 級進模即可把該零件沖制完成,在一副多工位級進模中
14、,可以連續(xù)完成沖裁、彎曲、拉深、成形等工序,一般級進模配以高速沖床,實現(xiàn)高速自動化作業(yè),能使沖床生產(chǎn)效率大副度提高。 條料在送進過程中應避免阻礙現(xiàn)象的產(chǎn)生:在設計多工位級進模條料排樣圖時,必須要確保在送料過程中自始至終通暢無阻,決不能有絲毫的障礙影響條料的運行,多工位級進模一般都采用浮動送料,使條料在整個沖制的送料過程中,浮離下模平面一定高度。 2.1沖壓工序在排樣設計中的順序原則 (1)對于純沖裁的多工位級進模,原則上先沖其形孔,并伴隨著沖切掉外形余料,最后得到一個完整的沖壓零件。 (2)凡屬于沖裁彎曲多工位級進模,應該先沖切掉孔和彎曲部分的外形余料,再進行彎曲,然后沖去其余的余料,
15、最后再沖那些靠近彎邊的孔和彎曲部分側面有空位精度要求的側壁孔。 (3)凡屬于沖裁拉深多工位級進模,從拉深直徑與拉深高度之比屬于多次拉深的零件,為保證材料流動,獲得較小拉深系數(shù),再加上切邊余量,應該先安排切口加工,再進行拉深,當拉深成形后,再從條料上沖下零件。 (4)對于零件帶有拉深、彎曲加工的沖壓零件,在設計條料排樣圖時,原則上是先拉深,然后再考慮沖邊的周邊余料,隨后進行彎曲加工。因為在拉深過程中,周圍材料的流動量是較大的,當拉深結束后在進行彎曲可以避免零件的變形。 彎曲、成形部位鄰近孔沖壓加工應考慮的問題:靠近彎曲部分的孔,應先加工孔后壓彎,這樣能簡化模具設計。如果孔的位置精度要求較高
16、,孔的形狀要求較嚴,先沖孔后壓彎就很難保證孔位精度(壓彎時必然引起孔的變形),為了保證孔位與孔形的正確,就應先沖孔,孔在壓彎時避免變形的條件為h>1.5t+r。屬于淺的擠出孔和鐓形加工,材料的流動對鄰近孔的影響是不可忽略的,這時應當先擠出孔、鐓形加工,然后再沖出鄰近孔。 2.2模具上應考慮的問題 (1)凹模應有足夠的強度:多工位級進模凹模的工作形孔以及其它各種安裝孔很多,因此在設計條料排樣圖時,必須全面考慮凹模強度,尤其在高速沖壓的場合下,形孔之間的最小間隔應適當,對于異形孔,其形孔間隔應適當放大一些。在設計排樣圖時,應避免形孔有尖的凸角、狹槽、細腰等微薄環(huán)節(jié),以保證凹模、凸模的強度。
17、(2)正確安排側刃孔與導正釘孔:側刃孔是用來控制步距的工藝性用孔,以便用它來保證每一工步的送進距離,所以側刃孔都安排在條料的第一工位。多工位級進模在采用自動送料機構送料時,必須在條料排樣圖的第一工位沖出工藝性導正釘孔,在第二工位及在以后每隔2—4工位的相應位置設置導正釘,對于某些圓形拉深件的多工位級進模,一般不必再設置導正釘,因為各工位的拉深凸模本身就對條料起到定距導正的作用,對于拉深成形以后再進行沖裁、彎曲等加工的零件,拉深階段同樣不必設置導正釘,導正釘孔的沖制放在拉深以后的工位,導正釘孔沖制以后的下一工位才開始設置導正釘。 2.3材料及其它問題 (1)被加工材料:多工位級進進模對被加工
18、材料的要求都是很嚴格的,在設計排樣圖時,對材料的供應狀態(tài)、被加工材料的機械性能、材料厚度、條料寬度、材料紋向以及材料的利用效率等都要予以全面考慮。例如材料的輾壓紋向,一個沖壓件當彎曲線與材料紋向垂直,壓出的零件質量穩(wěn)定光滑。當兩者平行時,對某些材料或彎曲半徑很小時,零件彎曲部分會出現(xiàn)裂紋。為此,帶有彎曲加工的級進模,在設計條料排樣圖時,應當保持零件彎曲線與材料輾壓紋向垂直。 (2)生產(chǎn)能力與生產(chǎn)批量:當企業(yè)的生產(chǎn)能力與生產(chǎn)批量相矛盾時,要力求采用雙排或多排排樣,在模具上提高效率;如果生產(chǎn)能力與生產(chǎn)批量相一致時,則以單排排樣為好。 (3)沖壓力的平衡:在設計條料排樣圖時,應考慮整個沖壓加工的
19、壓力中心力求與模具中心一致,不過有過大的差異。一般來說,模具中心與沖壓加工中心偏移最大不超過L/6。 (4)沖件的毛刺方向:當沖件圖紙?zhí)岢雒谭较蛞髸r,無論條料排樣圖是雙排還是多排,應保證各排沖出的零件毛刺方向一致,決不允許一副模具沖出的零件毛刺方向有正有反。 對于帶有彎曲加工的沖壓零件,在設計條料排樣圖時,應當使毛刺面留在彎曲件的內側,這樣不僅零件外形壓制美觀,而且彎曲部位不會出現(xiàn)邊口裂紋。在考慮分段切除余料時,不允許出現(xiàn)沖壓件周邊毛刺方向不一致的現(xiàn)象,可考慮某些部位進行側沖的措施來解決。 (5)步距精度與定距方式:多工位級進模的步距精度直接影響到?jīng)_壓件的精度,步距精度愈高,沖件精度
20、也愈高,但步距精度過高,模具制造也就愈困難,所以步距精度的確定必須根據(jù)沖壓件的具體情況,如沖件的精度等級、形狀復雜程度、沖件材質與厚度、模具工位數(shù)以及沖制時條料的送進方式等。定距方式有定位釘定距、側刃定距、自動送料機構定距以及導正釘定距幾種。定位釘定距適合于原料加工手工送料的普通級進模,模具的設計與制造均較簡單,但定位精度較低,因此大多作為一種輔助定距裝置使用。側刃定距是多工位級進模常用的一種定位方式,它適用于0.1—1.5mm厚的材料,對大于1.5mm或小于0.1mm的板料不宜采用。側刃定距是在條料的一側或兩側沖切定距槽,定距槽的距離等于步距長度。在多工位級進模中,通常以側刃作粗定位,以導正
21、釘作精定位??梢曰虻昧己玫亩ň嘈Ч_@時,側刃步距應稍大于實際步距0.04—0.12mm。導正釘定距是多工位級進模中極為普遍采用的定距方式,特別是形狀十分復雜的沖件,所采用的級進模一般采用這種方式定距,采用此種方式需要其它輔助定距方式配合,最常用的是以下兩種:1)一般沖床上用側刃作粗定距,導正釘作精定距,采用手工送料,進行加工。2)在高速沖床上,采用自動送料機構作粗定距,導正釘作精定距,以實現(xiàn)連續(xù)自動作業(yè)。 2.4 級進模的優(yōu)點 (1)級進模是多工序沖模,在一副模具內,可以包括沖裁、彎曲、成形和拉深等多種多道工序,具有比復合模更高的勞動生產(chǎn)率,也能生產(chǎn)相當復雜的沖壓件; (2)級進模操
22、作安全,因為人手不必進入危險區(qū)域; (3)級進模設計時,工序可以分散。不必集中在一個工位,不存在復合模中的“最小壁厚”問題。因而模具強度相對較高,壽命較長。 (4)級進模易于自動化,即容易實現(xiàn)自動送料,自動出件,自動疊片; (5)級進??梢圆捎酶咚賶毫C生產(chǎn),因為工件和廢料可以直接往下漏; (6)使用級進模可以減少壓力機,減少半成品的運輸。車間面積和倉庫面積可大大減小。 級進模的缺點是結構復雜,制造精度高,周期長,成本高。因為級進模是將工件的內、外形逐次沖出的,每次沖壓都有定位誤差,較難穩(wěn)定保持工件內、外形相對位置的一次性。但精度高的零件,并非全部輪廓的所有內、外形相對位置要求都高,
23、可以在沖內形的同一工位上,把相對位置要求高的這部分輪廓同時沖出,從而保證零件的精度要求。 第三章 制件成形工藝分析 工藝分析是制定工藝方案的基礎,它包括技術分析和經(jīng)濟分析兩方面內容。在技術方面,根據(jù)產(chǎn)品圖樣,主要分析該沖壓件的形狀特點、尺寸大小、精度要求和材料性能等因素是否符合沖壓加工的要求,即審查沖壓件的工藝性。在經(jīng)濟方面,主要根據(jù)沖壓件的生產(chǎn)批量,分析產(chǎn)品成本,闡明采用沖壓加工可以取得的經(jīng)濟效益。因此,沖壓件的工藝分析,主要是討論在滿足零件使用要求的前提下,能否以最簡單最經(jīng)濟的方法沖出零件,從而為制定工
24、藝方案奠定基礎。 沖壓件的工藝性系指沖壓件對沖壓工藝的適應性。在一般情況下,對沖壓件工藝性影響最大的是幾何形狀尺寸和精度要求。良好的沖壓工藝性應能滿足材料較省、工序較少、模具加工較易、壽命較高、操作方便及產(chǎn)品質量穩(wěn)定等要求。沖壓加工對沖壓件形狀和尺寸的要求:不同形狀和尺寸的沖壓件,需采用不同的沖壓加工方法,因此有不同的工藝要求。 沖壓加工對沖壓件精度的要求:沖壓加工與任何機械加工一樣,也有其自身的加工精度范圍。在實際生產(chǎn)中,由于影響沖壓加工精度的因子太多,因此對沖壓件的精度要求不宜過高。若精度要求過高,勢必給工藝設計、模具設計和制造都帶來困難,有時則須增加整形、整修等沖壓工序甚至機加工等工
25、序,才能達到工件的要求。沖壓件的精度一般可分為精密級與經(jīng)濟級兩類。精密級是指沖壓工藝在技術上所允許的最高精度,而經(jīng)濟級是指模具達到最大許可磨損時,其所完成的沖壓加工在技術上可以實現(xiàn)而在經(jīng)濟上又最合理的精度,即所謂經(jīng)濟精度。為降低沖壓成本,獲得最佳的技術經(jīng)濟效果,在不影響沖壓件使用要求的前提下,應盡可能采用經(jīng)濟精度。在本設計中,沖裁件的精度應達到精密級。 沖壓加工對沖壓件材料的要求:在沖壓件的工藝分析中,除對沖壓件的形狀、尺寸、精度進行工藝審查外,還應審查沖壓材料是否符合沖壓加工的工藝要求。沖壓材料與沖壓加工的關系十分密切,它直接影響沖壓生產(chǎn)和沖壓件質量。沖壓加工對沖壓材料的要求主要包括材料性
26、能和表面質量及厚度公差兩個方面。 沖壓加工對材料性能的要求:用于沖裁加工的材料,應具有足夠的塑性和較低的硬度,這有利于提高沖裁面的斷面質量和尺寸精度。軟材料(如黃銅)具有良好的沖裁性能,沖裁后可獲得斷面光滑和傾斜度很小的工件。硬材料(如高碳鋼,不銹鋼)沖裁后質量不好,斷面平面度很大,對厚板沖裁時尤為嚴重。對于脆性材料,再沖裁時易產(chǎn)生撕裂現(xiàn)象。 沖壓加工對材料表面質量和厚度公差的要求:用于沖壓加工的金屬板料,其表面應平整光潔,無劃痕,擦傷等缺陷。否則,在沖壓加工過程中,缺陷部位易產(chǎn)生應力集中而破壞,同時也影響沖壓件的外觀質量。當板料表面產(chǎn)生翹曲或不平時.則影響剪切加工,定位不準和損壞模具,使
27、廢品率增高。板料表面也不允許有銹斑,氧化皮及其它附著物,這不僅對沖壓加工不利,而且嚴重影響工件表面質量,且使模具壽命降低,同時又給后續(xù)加工帶來一定的困難。除上述的表面質量要求外,沖壓加工對板料厚度公差也有一定的要求。這是因為一定的模具間隙,適用于沖壓一定厚度的材料。如果板料厚度超差,不僅使沖壓件的表面質量和尺寸精度降低,而且也影響模具使用壽命,嚴重時會產(chǎn)生廢品及破壞模具。 本設計中的沖壓制件是甲烷電控單元支架零件。如圖3-1所示。 圖3-1 甲烷電控單元支架零件圖 工件名稱:甲烷電控單元支架 零件簡圖:如圖3-1所示 材 料:電工用工業(yè)純鉄(DT2)
28、厚 度:3mm 精 度:此產(chǎn)品為一支架,按IT12級確定工件尺寸的公差可滿足其工作的需要。 生產(chǎn)批量:大批量生產(chǎn) 材料分析:電工硅鋼板為黑色金屬,力學性能見下表3-1: 表3-1:DT2材料性能表 材 料 名 稱 材 料 狀 態(tài) 抗剪強度τ/MPa 抗拉強度σb/MPa 伸長率δ/% 屈服強度σs/MPa 電工用工業(yè)純鐵(DT2) 已退火 180 230 26 由制件零件圖可知:制件的外形規(guī)則,但需要經(jīng)過多次沖裁并彎曲才能完成加工;經(jīng)過總體分析,可采用少廢料的排樣方法。通過對零件的初步分析可知,要完成該制件的生產(chǎn),需要經(jīng)過以下的工藝
29、:沖孔、側刃切割、彎曲、切斷等工序。制件的厚度為3mm,沖壓件的材料是硅鋼。另外,在設計中還應該考慮到材料的沖裁工藝性,以及其纖維方向的特性。 3.1、工藝方案的制定 根據(jù)零件形狀確定沖壓工序類型和選擇工序順序,一般說來,一種較為合理的工序的選擇需要從沖裁件的生產(chǎn)批量,尺寸精度,形狀復雜程度,模具成本等多方面來考慮。沖模的典型結構有:單工序模、復合模、級進模。 單工序模:又稱簡單模,是指在壓力機的一次行程中,只完成單一工序的模具,如落料模、沖孔模、彎曲模和拉深模等。對于此產(chǎn)品來說,模具包含沖孔、落料、彎曲、和抽孔等,因此不適合用單工序模制造。 復 合 模:復合模是指在壓力機的一次行程內
30、在模具的一個工位上完成兩道以上沖壓工序的模具,是一種多工序沖壓模。常見的復合模,有落料和沖孔復合模、落料和首次拉深復合模等。復合模與單工序模相比,主要優(yōu)點是生產(chǎn)效率和沖壓件精度高,其缺點是模具結構復雜,不易制造。它適用于生產(chǎn)精度要求較高的軟材料或薄板料沖壓件。另外它的一個主要缺點是不能進行連續(xù)生產(chǎn),不便于自動控制。 級 進 模:也是一種多工序模,即在壓力機的一次行程中,在連續(xù)模具的不同工位上完成多道沖壓工序的模具,又稱連續(xù)摸。 根據(jù)甲烷電控單元支架的工藝分析,其基本工序可以有有沖孔、落料、切邊、彎曲三道基本工序,可得如下幾種方案; (1)沖孔——落料——彎曲;單工序模。 (2)沖孔落料
31、復合模——彎曲;復合模與單工序彎曲模沖壓。 (3)切邊——沖孔——彎曲——切斷;連續(xù)模沖壓。 方案(1)屬于單工序模沖裁工序,沖裁模指在壓力機一次行程內完成一個沖壓工序的沖裁模。,沖孔模、落料模以及彎曲模,由于此制件生產(chǎn)批量大,操作也不安全,所需要的勞動強度大,故不宜采用。 方案(2)屬于復合模與單工序彎曲模沖壓,是指先在復合模中形成基本的形狀,在通過彎曲模彎曲得到此產(chǎn)品,此套方案必須采取兩套模具,分別是復合模與單工序彎曲模,所以需要的成本也比較高,勞動強度大,由于此制件生產(chǎn)批量大因此,不宜采用該方案。 方案(3)屬于連續(xù)沖裁模,連續(xù)沖裁模是指在一次工作行程中,依次在模具幾個不同的位置
32、上同時完成多道沖壓工序。采用復合模沖裁,生產(chǎn)效率也很高,又降低的工人的勞動強度,所以此方案最為合適。 根據(jù)分析采用方案(3)連續(xù)沖裁。 3.2、 制件排樣、條料寬度及步距的確定 排樣是模具設計的核心部分,是級進模設計的重要依據(jù)。條料排樣圖的設計可以確定以下內容:第一,模具的工位數(shù)和各工位的工序內容;被沖制工件各工序的安排及先后順序;工件的排列方式;模具的步距、條料的寬度和材料的利用率;導料的方式和導正銷的安排;基本確定模具結構。排樣圖設計的好壞,對模具設計影響很大,因此要設計出多種方案進行比較,以選出最合理的方案。 3.2.1、排樣的選用原則 在設計排樣圖時,確定工位數(shù)在排樣圖設計中
33、,首先要考慮被加工零件在全部沖壓過程中要分幾個加工工序,并在其中設置幾個空位,在確定工位數(shù)時,要考慮到: 要保證沖件的精度要求和零件幾何形狀的正確。對于復雜的形孔與外形分段切除時,只要不受精度要求和模具周界尺寸的限制,應力求做到各段形孔以簡單、規(guī)則、容易加工為基本原則。 對于一些在普通低速沖床上沖壓的多工位級進模,為了使模具簡單、實用、縮小模具體積,或由于條料所限,甚至只能采用側刃做定位,為了減少步距的累積誤差,凡能合并的工位,只要能保證零件的精度,模具本身有足夠的強度,就不要輕易分解,增加工位。尤其對那些形狀不易分解的零件,更不要輕率增加工位。 在排樣圖中,增設空位工位的目的是為了保證
34、模具有足夠的強度,確保模具的使用壽命,或是為了便于模具設置特殊結構,用導正釘做精確定距的條料排樣圖可適當?shù)囟嘣O置空位工位。因步距累積誤差較小,對產(chǎn)品的精度不大。 當模具的步距較大時(一般步距>16mm),不宜設置空位工位。一般來說,精度高、形狀復雜的零件在設計條料排樣圖時,應該少設置空位工位;反之,形狀較簡單、精度低的零件可適當?shù)卦黾涌瘴还の弧? 工件排樣是沖壓工件及模具設計的重要環(huán)節(jié),它直接影響到材料的利用率、工件的質量、生產(chǎn)率、模具的制造難易程度、模具壽命等,排樣方式主要考慮的問題有: (1)材料的利用率:在滿足產(chǎn)品的質量要求的前提下,盡可能考慮高的材料利用率,材料的步距和料寬應取整數(shù)
35、。 (2)生產(chǎn)工藝性要求:產(chǎn)品形狀和排樣方式基本上決定了沖頭的形狀,所以在已定產(chǎn)品形狀的情況下,選擇排樣方式時就應該考慮沖頭的加工工藝性,使沖頭盡可能形狀最簡單,強度最大。沖頭形狀的設計應當考慮凹模的強度、沖頭的強度、沖頭的固定和沖頭的加工等各種因素。 為了使材料在沖壓過程中穩(wěn)定進給,必須在排樣中設置載體,并在連接處把工件和材料連接起來。載體一般設置在材料的兩側、中間部位或單側,載體的大小要有足夠的強度,又要節(jié)省材料。 帶有導正孔的載體能校正高速沖壓過程中的竄動。連接處的位置應選擇恰當,既要穩(wěn)定可靠,又要有利于其它工位和最后工位的切斷,與載體分離。 3.2.2、 排樣 根據(jù)材料經(jīng)濟利
36、用程度,排樣方法可以分為有廢料、少廢料和無廢料排樣三種,根據(jù)制件在條料上的布置形式,排樣有可以分為直排、斜排、對排、混合排、多排等多重形式。 采用少、無廢料排樣法,材料利用率高,不但有利于一次沖程獲得多個制件,而且可以簡化模具結構,降低沖裁力,但是,因條料本身的公差以及條料導向與定位所產(chǎn)生的誤差的影響,所以模具沖裁件的公差等級較低。同時,因模具單面受力(單邊切斷時),不但會加劇模具的磨損,降低模具的壽命,而且也直接影響到?jīng)_裁件的斷面質量。 由于設計的零件是矩形零件,,所以采用費料直排法。見下圖所示。 圖3-2 甲烷電控單元支架排樣圖 3.2.3、搭邊值的確定 排樣時零件之間以
37、及零件與條料側邊之間留下的工藝余料,稱為搭邊。搭邊的作用是補償定位誤差,保持條料有一定的剛度,以保證零件質量和送料方便。搭邊過大,浪費材料。搭邊過小,沖裁時容易翹曲或被拉斷,不僅會增大沖件毛刺,有時還有拉入凸、凹模間隙中損壞模具刃口,降低模具壽命。或影響送料工作。 搭邊值通常由經(jīng)驗確定,表所列搭邊值為普通沖裁時經(jīng)驗數(shù)據(jù)之一。 該制件是矩形工件,根據(jù)尺寸從《沖壓模實用設計手冊》中查出:鋼(WC0.05%~0.25%)兩制件之間的搭邊最小值a1=2.5(mm),側搭邊值a=2.8(mm)。 對于其他材料的應將表中的數(shù)值乘以下列數(shù): 鋼(WC0.3%~0.45%)
38、0.9 鋼(WC0.5%~0.65%) 0.8 硬黃銅 1~1.1 DT2 1~1.2 軟黃銅,純銅 1.2 由于該制件的材料是Q235,所以兩制件之間的搭邊值為: a1=2.5(1~1.2)=2.5~3(mm) 但考慮到凸模的強度問題取a1=5(mm) 側搭邊值 a=2.8(1~1.2)=2.8~3.36(mm) 取a=3(mm) 3.2.4、條料寬度的確定 計算條料
39、寬度有三種情況需要考慮; 有側壓裝置時條料的寬度。 無側壓裝置時條料的寬度。 有定距側刃時條料的寬度。有定距側刃時條料的寬度。 有側壓裝置的模具,能使條料始終沿著導料板一側送進。 條料寬度公式: B=(D+2a) 其中條料寬度偏差上偏差為0,下偏差為—△。 D——條料寬度方向沖裁件的最大尺寸。 a——側搭邊值。 查《沖壓模實用設計手冊》條料寬度偏差為0.9mm。 但此工件制作中涉及有彎曲的工部,所以有彎曲毛坯尺寸的計算,對于此工件而言,r=2,t=3,即r<0.5t.可由經(jīng)驗公式D=a+b+0.4t求得,
40、 其中在此工件總a=25mm,b=22mm,t=3mm代入上式有: D=(70+25)+22+0.4*3 =119.2mm 根據(jù)公式4 —1 B=(D+2a) =(119.2+23)0-0.9 =1250-0.9 3.2.5 導板間間距的確定 導料板間距離公式: A=B+Z Z——導料板與條料之間的最小間隙(mm); 查《沖壓
41、模實用設計手冊》得Z=2mm 根據(jù)公式 A= B+Z =125+2 =127(mm) 3.2.6材料利用率的計算: 沖裁零件的面積為: S= 15800(mm2) 送料步距為:h=L+a1=190+5=195mm 材料利用率大致可表示為: n11=(nS/Bh)100% 其中:n為一個步距沖裁零件數(shù)量; S為沖裁件的面積: B為條料的寬度: h為沖裁的步距。 代入公式有:
42、 n11=(nF/Bh)100% =(115800/133195)100% =60.9% 第四章 凹凸模形狀及尺寸的設計 4.1、凸凹模及彎曲模刃口形狀的確定 由制件展開圖(圖3-2)可以知道,要完成制件的加工,需要將帶料上的廢料沖裁掉,各工位沖裁掉廢料的外觀形狀即為凹模、凸模的刃口形狀;對于沖孔凸模,展開圖中所取的目標值即為凸模刃口的形狀尺寸。對于制件外觀形狀不規(guī)則部分的成形,其成形凸模、凹模叫做異形凸模或者異形凹模。異形凹模或凸模的刃口形狀沒有固定的設計標準,在滿足制件外形的情況下刃口形狀可
43、以自己確定,但必須考慮以下條件:查《沖壓模具設計實用手冊》,當料厚為0.5mm時,異形凹模、凸模的最小寬度應該大于2mm;在設計中,通常確定最小尺寸的方法是,異形凸模最小寬度 形狀應該力求簡單,以利于材料的合理利用,同時要避免細長懸臂結構;轉角處要盡量避免尖角,尖角處應該用圓弧連接,以起到避免尖角處因應力集中而使沖模裂開的危險。對于此設計中的材料,其最小圓角半徑的選取標準為: 落料部分:當圓弧角大于或等于90度時,最小圓角半徑=0.25T;當圓弧角小于90度時,最小圓角半徑=0.5T; 沖孔部分:當圓弧角大于或等于90度時,最小圓角半徑=0.30T;當圓弧角小于90度時,最小圓
44、角半徑=0.6T。 各凸模從左到右刃口大致形狀如下示意圖: 圖4-1 凸模一刃口示意圖 圖4-2 凸模二刃口示意圖 圖4-3 凸模三刃口示意圖 圖4-4 凸模四刃口示意圖 圖4-5 凸模五刃口示意圖 圖4-6 凸模六刃口示意圖 4.1 、沖裁間隙的確定 4.1.1、 凹模、凸模間隙的確定 沖裁模的凸模橫斷面,一般小于凹模孔,凹模與凸模部分,在垂直沖裁方向的投影尺寸之差,叫做沖裁間隙。沖裁間隙有兩種含義:一種是指凹模與凸模間每側空隙值,稱為單面
45、間隙;另外一種指凹模和凸模間兩側間隙之和,稱為雙面間隙;習慣上常說的間隙是指雙面間隙,用符號Z表示,單面間隙用Z/2表示。 生產(chǎn)實踐證明,間隙值的大小,分布均勻與否,對沖裁件的斷面質量、尺寸精度、沖裁力和模具壽命有直接的影響。凸模和凹模之間的大小可以分為三種基本情況,即間隙合理,間隙過大,間隙過小三種情況。 沖裁間隙的大小對制件斷面的影響,間隙合理,材料在分離時,凹模和凸模刃口處裂紋重合,沖裁間隙不是一個絕對值,而是一個數(shù)值范圍,沖裁間隙在此范圍內都可以得到?jīng)_裁斷面較好的制件;間隙過大,凸模和凹模刃口處的裂紋不重合,凸模刃口附近的裂紋在凹模刃口附近裂紋的里邊,材料受很大的拉伸,光亮帶小,毛
46、刺、塌角及斜度都比較大;間隙過小,裂紋也不重合,凸模刃口附近的裂紋在凹模刃口附近裂紋的外邊,兩條剪裂紋之間的一部分材料隨沖裁的繼續(xù)又被二次剪切和擠壓,在斷面上形成第二次光亮帶,并在中間出現(xiàn)夾層和毛刺。 (1)沖裁間隙對制件尺寸精度的影響 落料和沖孔后,因發(fā)生彈性恢復,會影響制件的尺寸精度。沖裁間隙小到一定程度時,由于壓縮變形彈性恢復,落料件的尺寸會大于凹模尺寸,而沖出的孔小于凸模。間隙大到一定界限時,由于拉伸變形的彈性恢復,落料尺寸會小于凹模的刃口尺寸,而沖出的孔會大于凸模的刃口尺寸。間隙對于沖孔和落料精度的影響規(guī)律是不同的,且和材料的纖維方向有關。 (2)沖裁間隙對沖裁力和模具壽命的
47、影響 間隙大時,沖裁力有一定的程度減小,卸料力和推件力也隨之降低。沖裁時,坯料對凹模凸模產(chǎn)生側壓力,并在凸磨與被沖孔之間及凹模與落料件之間均有摩擦力。間隙越小摩擦力和側壓力隨之增大。此外,由于在實際的生產(chǎn)中,模具因受到制造誤差和裝配精度的限制,凸模和凹模不可能絕對的垂直于凹模平面,而間隙的分布也不可能十分均勻。所以,過小的間隙會使凸模和凹模刃口的磨損加劇,使模具的使用壽命下降。而較大的間隙則可以使凸模和凹模側面與材料間摩擦減小,并且可以減小間隙不均勻的不利影響,從而提高模具的壽命;但間隙過大 ,坯料彎曲變形相應的增大,使凸模與凹模刃口端面的壓應力分布不均勻,容易產(chǎn)生崩刃或塑性變形。因此,過
48、大的刃口間隙對模具的壽命也不利。 沖裁時由于凸模和凹模之間存在間隙,因此落下的料或者沖出的孔均帶有錐度,其大端尺寸基本等于凹模尺寸,小端尺寸基本等于凸模尺寸。測量時也是按沖孔的小端和落料的大端作為基準尺寸。由于在生產(chǎn)中,凸模和凹模都要與沖件或廢料產(chǎn)生摩擦,凸模會越變越小,凹模會越來越大,基于這一分析,確定沖裁間隙的原則為:落料時因為制件尺寸隨凹模尺寸而定,故間隙應該在減小凸模尺寸方向取得;沖孔時由于孔的尺寸隨凸模尺寸而定,故間隙應該在增大凹模尺寸的方向上取得??紤]到凸模和凹模的磨損,在設計和制造新模具時,取最小合理間隙。 4.2.2、 確定沖裁間隙的方法 常用的沖裁間隙確定方法有理論
49、確定法和經(jīng)驗確定法。經(jīng)驗計算公式為: 式中 :C——合理沖裁間隙(mm); t——板料厚度(mm); m——系數(shù),與料厚及材料性質有關,m通常為料厚的百分之幾。沖裁間隙系數(shù)如下表所示,選至《中國模具設計大典》 單位:mm 表4-1 沖裁間隙系數(shù)m 材 料 抗拉強度 /Mpa 間隙類別 Ⅰ Ⅱ Ⅲ 低炭鋼 08F、DT2、10、20、Q235-A ≥210~400 3~7 7~10 10~12.5 中炭鋼45不銹鋼 1Cr18Ni9Ti ≥420~560 3.5~8 8~11 11~15 高炭鋼 T
50、8A T10A 65Mn ≥590~930 8~12 12~16 16~18 電工硅鋼D21、D31、D41 190 2.5~5.0 5~9 材料Q235的抗剪強度為210~400Mpa,其沖裁間隙值可以在上表中參照抗剪強度與之相近的材料的沖裁間隙系數(shù)進行選取,同時為了達到客戶對零件精度的要求,選取Ⅰ類間隙,為了使沖裁截面質量較好和在沖孔直徑非常小時,部分間隙值還可以值適當?shù)目s小,則凹模和凸模之間的間隙范圍為: 最小間隙 C=mt=3%3=0.09mm; 最大間隙 C=mt=7%3=0.21mm。 4.3 、凸凹模刃口尺寸的計算 4.3.1 、尺寸
51、公差確定原則 由于沖裁時,凸凹模零件要與沖壓工件或廢料發(fā)生摩擦,凸模越磨越小,凹模越磨越大,結果使得凸凹模間隙越來越大。在沖裁件尺寸的測量中和使用中,都是以光面的尺寸為基準的。落料件的光面是因凹模刃口擠切材料產(chǎn)生的,而孔的光面是凸模刃口擠切材料產(chǎn)生的。故計算刃口尺寸時,因按落料和沖孔兩種情況分別進行,其原則如下: (1)落料時,因落料件光面尺寸與凹模尺寸相等(或基本一致),應先確定凹模尺寸,即以凹模尺寸為基準。又因落料
52、件尺寸會隨凹模刃口的磨損而增大,為保證凹模磨損到一定程度仍能沖出合格零件,故落料凹?;境叽鐟」ぜ叽绻罘秶鷥鹊妮^小尺寸。而落料凸?;境叽鐒t按凹模尺寸減最小初始間隙。 (2)沖孔時,因工件光面的孔徑與凸模尺寸相等(或基本一致),就先確定凸模尺寸,即以凸模尺寸為基準。又因沖孔的尺寸會隨凸模的磨損而減小,故沖孔凸模基本尺寸應取工件孔尺寸公差范圍內的較大尺寸。而沖孔凹模基本尺寸則按凸?;境叽缂幼钚〕跏奸g隙。 (3)確定沖模刃口制造公差晨,應根據(jù)沖裁件的公差要求。如果沖模制造公差過小,會使模具制造困難,增加成本,延長生產(chǎn)周期;若沖模制造公差過大,則工件可能不合格,沖模壽命降低。 4.3.
53、2 凸凹模一刃口尺寸的計算 凸模一(圖4-1)主要是起切邊的作用,所以在沖裁過程中對精度要求不要,板料精度為IT12,查《沖壓模具設計實用手冊》得此刃口精度為IT9。A=8mm, =198mm查得即K分別為1和0.75。△分別為0.15和0.46 凸模尺寸:A = (A+K△) =(8+10.15)0-0.036 = 8.150-0.036(mm) = (A+K△) =(198+0.750.46)0-0.115
54、 = 198.350-0.115(mm) 凹模尺寸: a = (A+Z) =(8.15+0.09) = 8.24 (mm) = (A+ Z) =(198.35+0.09) = 198.35 (mm) 4.3.3 、凸凹模二刃口尺寸的計算 凸模二(圖4-2)主要是起沖裁的作用,板料精度為IT12,查《沖壓模具設計實用手冊》得此刃口精度為IT9。B=30mm, =130mm查得即K分別為1和0.75?!鞣謩e為0.121和0.
55、4 凸模尺寸:B = (B+K△) =(30+10.21)0-0.052 = 30.210-0.052(mm) = (B+K△) =(130+0.750.4)0-0.1 = 130.3 0-0.1(mm) 凹模尺寸: b = (B+Z) =(30.21+0.09) = 30.3 (mm) b= (
56、B+ Z) =(130.3+0.09) = 198.35 (mm) 4.3.4 、凸凹模三刃口尺寸的計算 凸模三(圖4-3)主要是起沖裁的作用,板料精度為IT12,查《沖壓模具設計實用手冊》得此刃口精度為IT9。由于此凸模僅三尺寸最為影響工件的精度即C=25mm, =120mm,=49.2mm查得即K分別為1,0.75和0.75。△分別為0.21,0.35和0.25 凸模尺寸: C = (C+K△) =(25+10.21)0-0.052 = 25
57、.210-0.052(mm) C= (C+K△) =(120+0.750.35)0-0.87 = 120.26 0-0.87(mm) C = (C+K△) =(49.2+0.750.25)0-0.062 = 49.390-0.062(mm) 凹模尺寸: c = (B+Z) =(25.21+0.09) = 2
58、5.30 (mm) c= (B+ Z) =(120.26+0.09) = 120.35 (mm) c= (B+ Z) =(49.39+0.09) = 49.48 (mm) 其他尺寸凸模均按h9,凹模均按H9。 4.3.4 、凸凹模四刃口尺寸的計算 凸模四(圖4-4)主要是起沖裁的作用,板料精度為IT12,查《沖壓模具設計實用手冊》得此刃口精度為IT9。此凸模直徑D=6.5mm,查得即K為1?!鞣謩e為0.15。兩凸模距離L,L分別為173.5mm和4
59、0mm 凸模尺寸:D =(D+K△) =(6.5+10.15)0-0.036 = 6.650-0.036(mm) 凹模尺寸: d = (D+Z) =(6.65+0.09) = 6.74 (mm) 凹模孔之間的距離分別為:L=( L+△) T =(173.5+0.4)0.05 =173
60、.70.05(mm) L=( L+△) T =(40+0.25)0.03 =40.130.05(mm) 4.3.6 、凸凹模五刃口尺寸的計算 凸模五(圖4-5)主要是起沖裁的作用,板料精度為IT12,查《沖壓模具設計實用手冊》得此刃口精度為IT9。此凸模直徑D=8.5mm,查得即K分別為1?!鳛?.15。兩凸模距離S,分別為156mm 凸模尺寸:E =(E+K△)
61、 =(8.5+10.15)0-0.036 = 8.650-0.036(mm) 凹模尺寸: e = (e+Z) =(8.65+0.09) = 8.74 (mm) 凹模孔五中心距為:S=( S+△) T =(156+0.4)0.05 =156.50.05(mm) 4.3.7 、凸凹模六刃口尺寸的計算 凸模六(圖4-6)主要是起切斷的
62、作用,板料精度為IT12,查《沖壓模具設計實用手冊》得此刃口精度為IT9。此凸模尺寸F=5mm,其他尺寸不考慮,查得即K分別為1?!鳛?.12。 凸模尺寸:F =(F+K△) =(5+10.12)0-0.03 = 5.120-0.03 (mm) 凹模尺寸: f = (f+Z) =(5.12+0.09) =5.21 4.4、彎曲模的設計 彎曲V形件時,不需要在設計和制造模具時確定間隙。此彎曲件為L型彎曲,對于L形件的彎曲,必須
63、選擇合模具間隙 彎曲L形件時,凸、凹模間隙是用調整沖床的閉合高度來控制的適的間隙,間隙過小,會使邊部壁厚變薄,降低模具壽命。間隙過大則回彈大,降低制件精度凸、凹模單邊間隙Z一般可按下式計算: Z=t+Δ+ct 式中:Z——彎曲凸、凹模單邊間隙 t——材料的厚度 Δ——材料厚度的正偏差;Δ =0 C——間隙數(shù)查表得,查《沖壓模具設計實用手冊》得C=0.08 則 Z=t+Δ+ct =3+0+0.083
64、 =3+0.24 =3.24 (mm) 注:彎曲件經(jīng)沖裁后會有一定的回彈值,經(jīng)查《沖壓模具設計實用手冊》此次彎曲回彈值大致1~2??紤]到此產(chǎn)品的精度要求,可以忽略其回彈值。另外規(guī)定彎曲凹模R=2mm,經(jīng)查表可知凸模r=(2~3)t,取r=6mm。 第六章 力的計算和沖壓設備的選用 6.1 力的計算 計算沖裁力的目的是為了選擇合適的壓力機,設計和檢驗模具的強度。壓力機的噸位必須大于所計算的沖裁力,以適應
65、沖裁工藝的需求。 工序—為沖裁,該工序沖壓力包括沖裁力F,卸料力F和推料力F,考慮此模巨的結構形式,不需要頂件結構,故不考慮頂件力F。但還必須考慮彎曲力F用一般平刃口的凸模和凹模進行 計算沖裁力的目的是為了合理地選用沖床和設計模具,沖床的噸位必須大于所計算的沖裁力,以適應沖裁的要求。 一般情況下,選擇壓力機噸位時,應將沖裁力乘以安全系數(shù),其值一般取1.3。 1.沖裁力 沖裁時,其沖裁力可以按下面公式計算: F=KLtτ 式中 F——沖裁力(N) τ——材料抗剪強度Mpa L——材料輪廓長度(mm) t——材料厚度(mm) 對于四個工位而
66、言,沖裁的總長度為 L=L+L+L+4*L+2*L+L =412+320+600.4+4*20.41+2*26.69+162 =1629.42mm 則:F=1.3*1629.42*3*180 =1143853(N) 2. 卸料力 F=KF =0.03*F =34315(N) 式中:K——頂件力系數(shù);查表得0.03。 F——沖裁力;N 3. 推料力 F=KF =0.045*F =51473(N) 式中:K——頂件力系數(shù);查表得0.05。 F——沖裁力;N 4、彎曲力 F= =0
- 溫馨提示:
1: 本站所有資源如無特殊說明,都需要本地電腦安裝OFFICE2007和PDF閱讀器。圖紙軟件為CAD,CAXA,PROE,UG,SolidWorks等.壓縮文件請下載最新的WinRAR軟件解壓。
2: 本站的文檔不包含任何第三方提供的附件圖紙等,如果需要附件,請聯(lián)系上傳者。文件的所有權益歸上傳用戶所有。
3.本站RAR壓縮包中若帶圖紙,網(wǎng)頁內容里面會有圖紙預覽,若沒有圖紙預覽就沒有圖紙。
4. 未經(jīng)權益所有人同意不得將文件中的內容挪作商業(yè)或盈利用途。
5. 裝配圖網(wǎng)僅提供信息存儲空間,僅對用戶上傳內容的表現(xiàn)方式做保護處理,對用戶上傳分享的文檔內容本身不做任何修改或編輯,并不能對任何下載內容負責。
6. 下載文件中如有侵權或不適當內容,請與我們聯(lián)系,我們立即糾正。
7. 本站不保證下載資源的準確性、安全性和完整性, 同時也不承擔用戶因使用這些下載資源對自己和他人造成任何形式的傷害或損失。
最新文檔
- 2023年六年級數(shù)學下冊6整理和復習2圖形與幾何第7課時圖形的位置練習課件新人教版
- 2023年六年級數(shù)學下冊6整理和復習2圖形與幾何第1課時圖形的認識與測量1平面圖形的認識練習課件新人教版
- 2023年六年級數(shù)學下冊6整理和復習1數(shù)與代數(shù)第10課時比和比例2作業(yè)課件新人教版
- 2023年六年級數(shù)學下冊4比例1比例的意義和基本性質第3課時解比例練習課件新人教版
- 2023年六年級數(shù)學下冊3圓柱與圓錐1圓柱第7課時圓柱的體積3作業(yè)課件新人教版
- 2023年六年級數(shù)學下冊3圓柱與圓錐1圓柱第1節(jié)圓柱的認識作業(yè)課件新人教版
- 2023年六年級數(shù)學下冊2百分數(shù)(二)第1節(jié)折扣和成數(shù)作業(yè)課件新人教版
- 2023年六年級數(shù)學下冊1負數(shù)第1課時負數(shù)的初步認識作業(yè)課件新人教版
- 2023年六年級數(shù)學上冊期末復習考前模擬期末模擬訓練二作業(yè)課件蘇教版
- 2023年六年級數(shù)學上冊期末豐收園作業(yè)課件蘇教版
- 2023年六年級數(shù)學上冊易錯清單十二課件新人教版
- 標準工時講義
- 2021年一年級語文上冊第六單元知識要點習題課件新人教版
- 2022春一年級語文下冊課文5識字測評習題課件新人教版
- 2023年六年級數(shù)學下冊6整理和復習4數(shù)學思考第1課時數(shù)學思考1練習課件新人教版